Why not go for a concrete kimono?
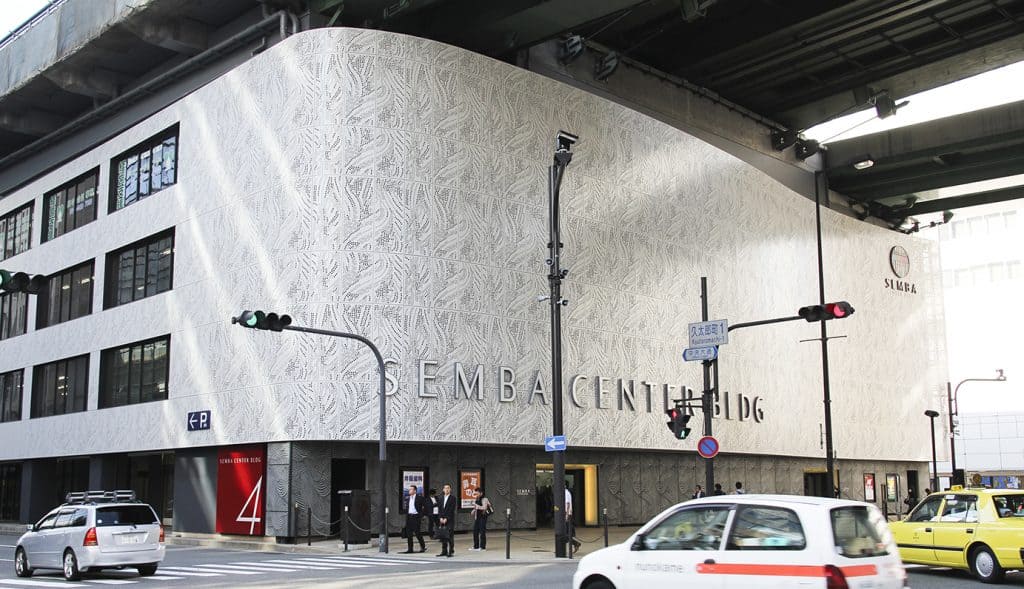
The mammoth-sized textile centre in the heart of Osaka, Japan, is an inspiring example of the endless possibilities of precast concrete. The facade of the unattractive complex was rejuvenated by seven traditional kimono patterns using graphic concrete, a patented technology invented by interior architect Samuli Naamanka.
The innovative graphic concrete is conquering new markets. Already well established in the Nordic countries, graphic concrete is now raising awareness in countries such as Japan of unique ways to enhance the built concrete environment.
Graphic concrete enables durable patterns and images to be produced on prefabricated concrete surfaces such as facades, walls, and pavement slabs. The desired image is printed on the membrane with a surface retarder, after which the membrane is sent to the local concrete prefabrication company.
Fusion of urban look and traditional patterns
In Japan, the impressive concrete artwork originates from the meeting of architect Naamanka and Yoshihiro Tada, the Chief Architect of the Ishimoto Architectural & Engineering Firm, which was selected to carry out a renovation project for the Semba Center Building. Architects were assigned to maintain the urban look of the bazaar-like complex of ten buildings while at the same time highlight the textile activities inside.
Architects at Ishimoto were inspired by the poetic idea of somehow incorporating a traditional kimono pattern. After designing their own sketches of the pattern, a more artistic touch was still needed. As a fortunate coincidence, fiber concrete manufacturer AGB presented the graphic concrete technique to Ishimoto’s architects just in time, shortly before Mr. Tada’s visit to Finland.
It only took one day for Samuli Naamanka to convince Mr. Tada that graphic concrete was the right choice for the new façade of the Semba Center Building. Samuli Naamanka was asked to design the final pattern. The outcome was seven different patterns for the facade, created using graphic concrete and perforated aluminum panels.
“This was a remarkable work for me, it really inspired me,” says Naamanka.
Safe production process without solvents
Graphic concrete is a patented technology in industrialized western countries and China. The biggest market areas for the technology are currently Finland, Sweden, and Denmark. Interesting new fields are on the horizon, however.
Naamanka and Graphic Concrete Ltd, the company that manufactures and sells the innovative product, have already made initial visits to China, where the creative possibilities of precast concrete building have been noted. As for the United States, the first reference case has been carried out together with world-famous architect firm Foster + Partners. In their work, curved graphic concrete was utilized to intensify the visual effect of the Project Honor in the SC Johnson Fortaleza Hall.
The idea behind graphic concrete technology is to create a real industrial product for large-scale surfaces. In Finland, where the technology originated, graphic concrete is already a standardized part of the prefabrication industry and is thus easy to use. Graphic concrete can be applied to any type of concrete surface: sandwich concrete, large-panel concrete, and fiber-reinforced concrete, to mention just a few.
The cost-effectiveness of the material is obvious: the surface is ready as such and needs no more cladding. Moreover, savings can be achieved in production.
“Comparing to exposed-aggregate finishing, the dry membrane of graphic concrete accelerates mold circulation by twenty percent,” Naamanka says.
“Even more importantly, the production process is environmental friendly and safe as no solvent-based materials are needed. Cleaning the mold is also less dusty.”
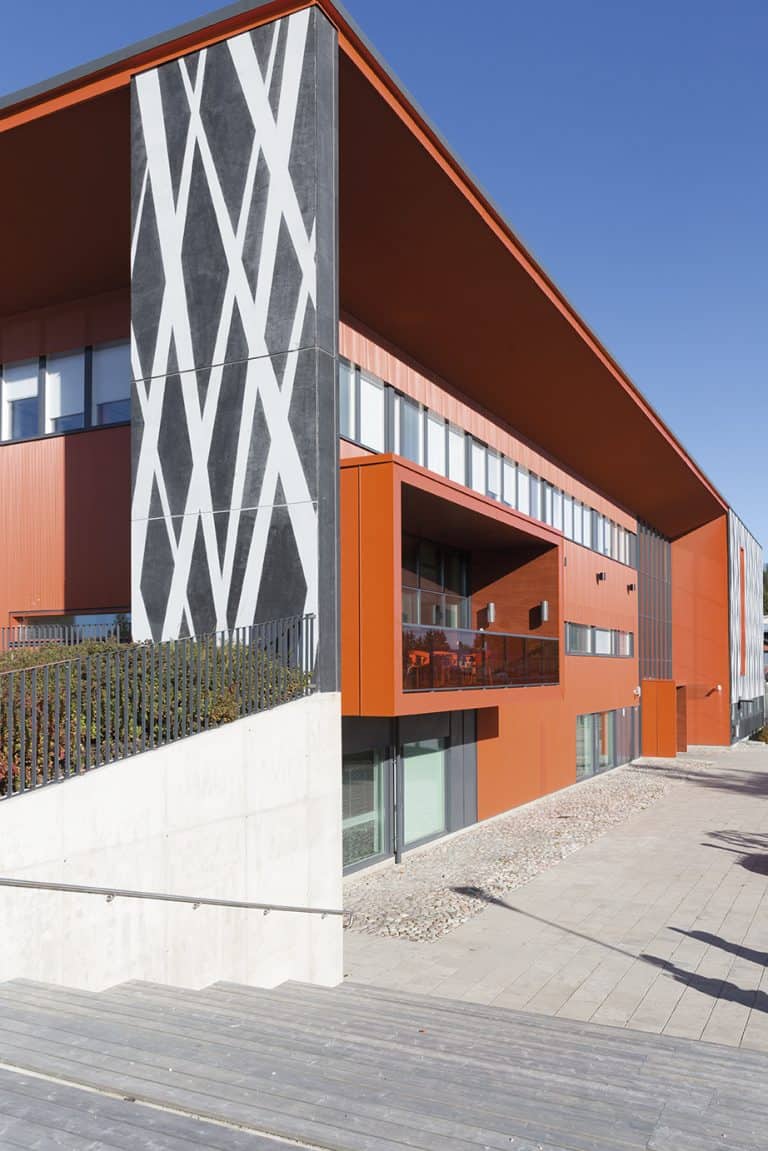
More beauty with graphic concrete
Samuli Naamanka’s inspiration with graphic concrete was to create a tool to enable architects to be more visually creative. Numerous examples of this creativity are visible in cities and suburban areas in Finland and other Nordic countries, where precast concrete construction has been popular since the 1970s.
Naamanka points to Ulappatori, a Finnish residential building, as a typical example of how graphic concrete can be used to create a fresh image for a traditional precast concrete building. The organic patterns were used in the entire facade to create new type of environment for the urban redevelopment project. The imposing architectural solution has created a popular landmark in the community.
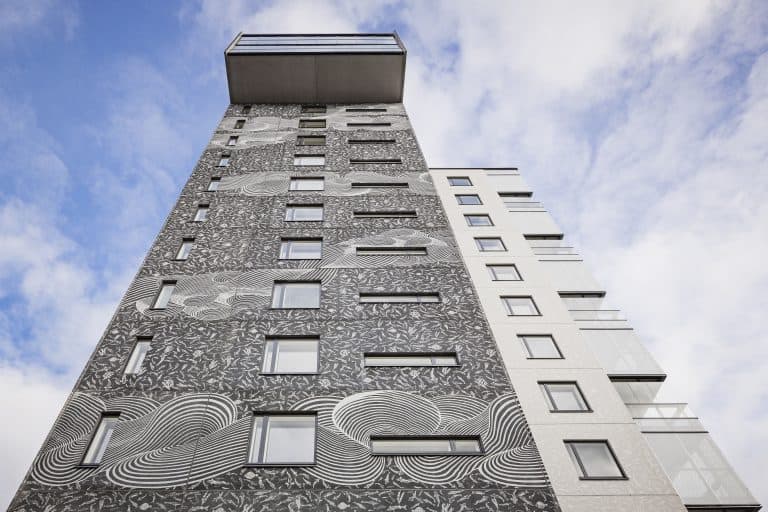
“The organic patterns, inspired from the site’s proximity to the sea, soften the massive scale of the buildings. This is a good example of the way that graphic concrete brings about interesting facades very cost-effectively. Comparing to other precast concrete buildings at close quarters, the graphic concrete facade added a totally new dimension to Ulappatori,” Naamanka describes.
The building received an award at the German Design Council’s cross-disciplinary architectural competition, 2014 Iconic Awards.
Interior architect Samuli Naamanka is known as a versatile designer who utilizes creative technical innovations in his work. Besides being a distinguished product designer and interior designer, Naamanka has carried out groundbreaking work in the development of concrete products, including patented inventions for a graphic concrete patterning technology and for coloring concrete in several different colors.
In 2015, Naamanka received the prestigious Finnish Asko Avonius Award for his exceptionally wide-ranging skills and keen interest in different ways of living, scales and materials.
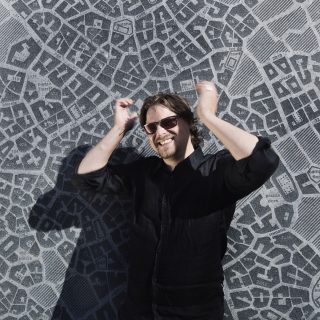
“Giving an unsightly, centrally located complex an interesting facade really enhances the urban environment. It has been wonderful to hear about the surprise and delight of passersby when they notice the new look of the Semba Center Building.”
Production process of graphic concrete
- 1. The designer designs a pattern or selects one from the Graphic Concrete collection. The designer sends the pattern to Graphic Concrete.
- 2. The pattern is printed onto a membrane and the membrane is sent to the concrete element producer.
- 3. The membrane is placed on the bottom of the mold. Concrete is poured into the mold.
- 4. The membrane is removed from the surface of the element the next day. The surface is cleaned with high-pressure water.
- 5. The element and the graphic concrete pattern are ready.