The birthplace of Green quality
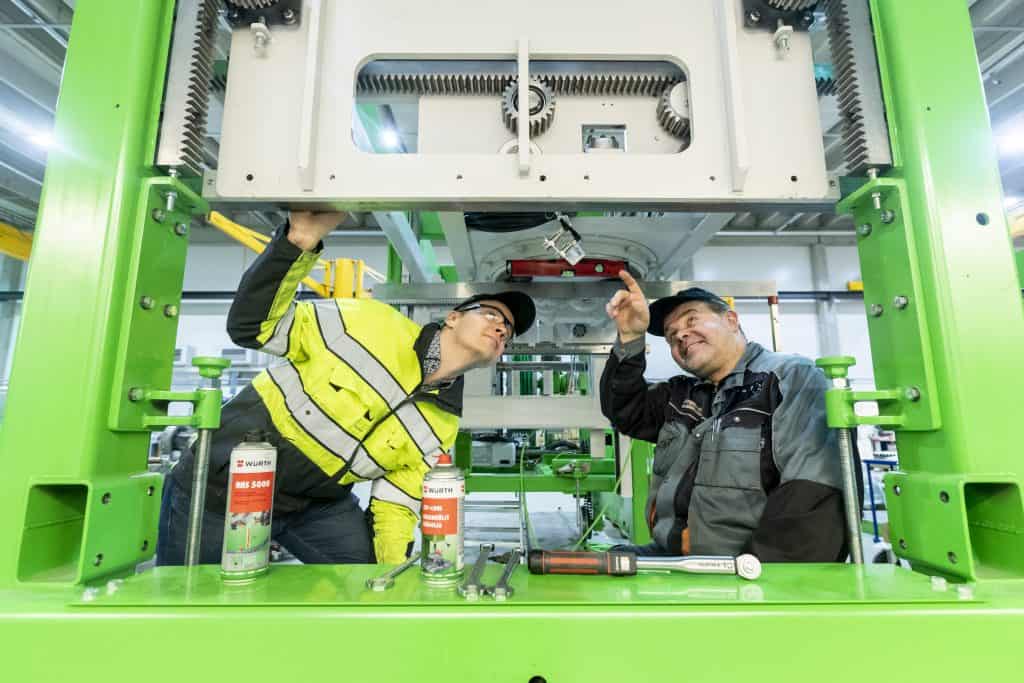
Have you ever wondered where your precast concrete machinery comes from? Let’s take a round tour in Elematic’s assembly unit.
Staff wearing overalls, safety glasses, caps and boots are working in a production hall in a practiced manner. These mechanics and electricians know how to make Extruders, Modifiers, and Acotec wall panel production lines. Modules are assembled, machines electrified, and dozens of details are measured and tested here. Magnets for wall production are also manufactured in this hall.
Elematic has two production units in Finland. The one in Riihimäki is a steel element producing plant where mold production, painting and welding take place, but this production unit in Akaa is a machine assembly unit which was opened in 2015 next to Elematic’s headquarters. Of course, production existed before these new facilities.
Making 20 machines a month
Painted, welded and machined parts from about 200 suppliers enter the production hall through a large door in one end, and ready-to-use machines exit the hall from another door on the opposite end.
About twenty machines are assembled in this unit every month. Assembly times vary a lot, from 50 hours to over 500 working hours, depending on the type of the machine. Complete machines are shipped all over the world, to different parts of Europe, The Middle East, Asia, and North America.
The production hall resembles a Tetris game with a constant incoming flow of suppliers’ parts and an outgoing flow of products to precasters who need to receive their new machines on time.
“One of the most important and challenging parts in my job is to make sure that we are always on schedule. We must get the incoming parts on time, the machines must hit their destination in time, and the quality of the components must meet the set requirements”, says Mika Rantasalo, Production Manager, assembly.
Once a machine is ready and tested, it is packed and sent to the factory who placed the order. Functional logistics and discharging are also parts of good service.
“We aim to serve precasters as well as we can. We make all settings and adjustments which can be made here so that the start-up of a machine will be as easy as possible at the factory. I am proud of my team and the good team spirit we have here. The way people share their assembly knowhow with their teammates is especially great”, Rantasalo says.
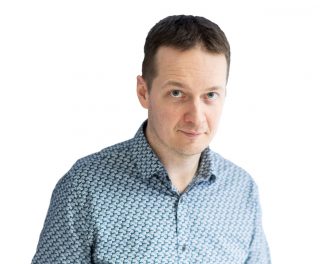
Mika Rantasalo, Production Manager, Assembly
Akaa Production Unit
- Machine assembly unit
- Number of staff: 32
- About 20 machines are assembled here every month. The length of different projects varies typically from 50 to 500 working hours.
- The machines assembled here include Extruders (for hollow-core slab production), Modifiers (for making recesses and openings), hollow-core slab saws, Preparers (for oiling and brushing beds), shuttles for concrete transportation, Acotec partition wall production lines, push-button magnets for shuttering systems, Plotters (large inkjet printers), Loopers, and twin shaft mixers.
- Comcasters (for wall element production) and Framecasters (for beam production) are assembled here occasionally.
- Ready products are shipped all over the world.
Taking pride in craftsmanship
A dedicated team of mechanics and electricians ensures the quality and functionality of your machines.
1. What is the most challenging part in the machine you are assembling?
2. What are you proud of in your work?
Heikki Hell, mechanic
1. I am assembling the nozzle unit of an Extruder. The most challenging part is making the inside of the gearbox. You must be very precise to ensure good quality.
2. I take pride in the fact that only top-notch products leave this unit. We get hardly any reclamations.
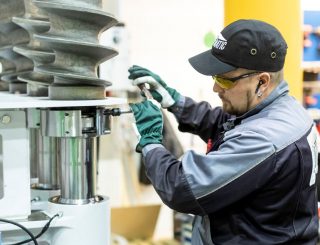
Heikki Hell, mechanic
Teija Heikkilä, electrician
1. I am equipping a baseplate of a switchgear for a concrete mixing plant. With 12 years of experience, I know all the working stages inside and out.
2. I am proud that my craftsmanship shows in the final product. I start with a clean table and create a product that works. That makes me feel like I have succeeded.
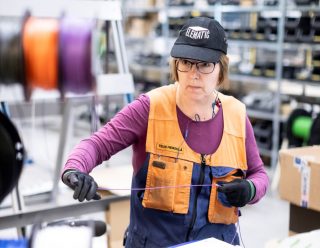
Teija Heikkilä, electrician
Mika Uusitalo, mechanic
1. I am doing quality control for a hollow-core slab saw: I am ensuring that a side transfer wagon is even-keel. You must be alert in all stages.
2. I am proud of being able to improve machine quality with my own hands.
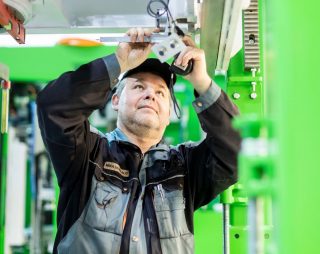
Mika Uusitalo, mechanic
Order our newsletter or contact us
or