From the safety of machines towards system safety
Increased automation minimizes the physically heavy, repetitive, and high-risk work phases, and makes production more flexible and efficient. “However, automated machinery and equipment also create new types of risks that need to be taken into consideration when planning maintenance or handling unexpected situations in production”, says Risto Tiusanen, Senior Scientist at VTT Technical Research Centre of Finland Ltd.
In the EU, for example, safety requirements have been dictated by the Machinery Directive and related standards since 1995. “All leading component manufacturers and system suppliers today consider safety issues to be business critical.”
The safety of machines, including safety guards or beams, sensors, and other protection systems, is generally on an advanced level. “This is not enough since the growing trend towards unmanned production in all branches calls for software-based solutions to operate the entire manufacturing system safely and efficiently. We have moved from the safety of machines to a level of system safety”, Tiusanen concludes.
Current issues in system safety
Perception: The system identifies the location of operators or maintenance personnel and optimizes production flexibly without downtime.
Communication: The increasingly complex systems demand reliable and secure channels to deliver critical data and signals.
Openness: Taking safety issues into account at the initial concept design phase or when planning a retrofit – system safety and reliability are created in cooperation with the end user, maintenance, and the equipment supplier.
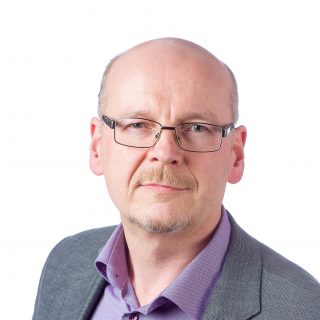
Risto Tiusanen