Rest assured with
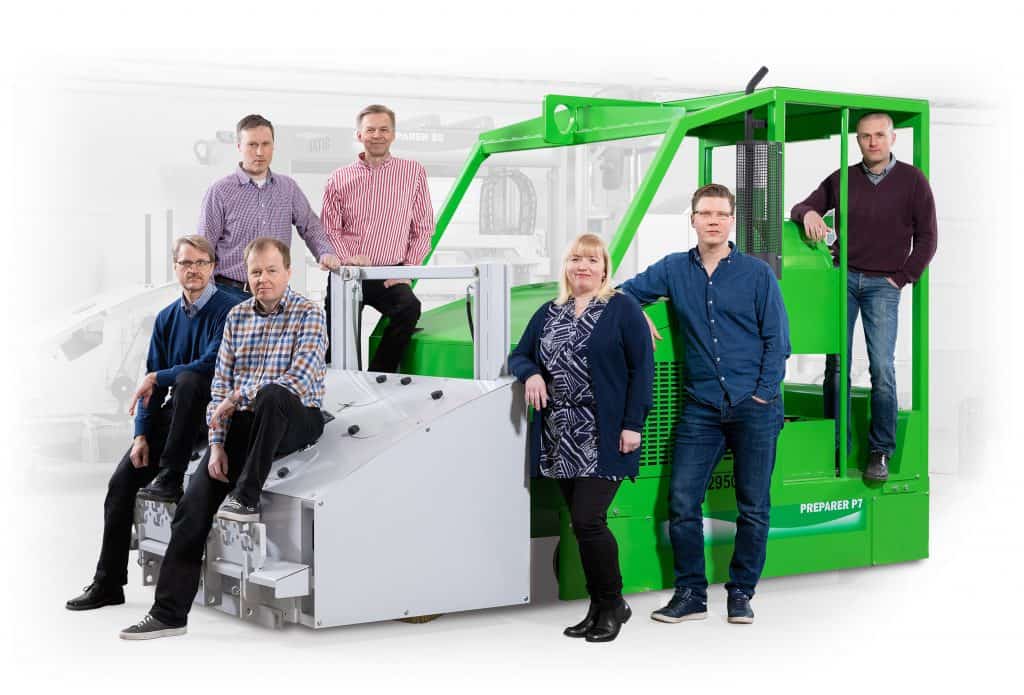
The time has come to increase your precast factory capacity, start manufacturing new products, increase automation, or even etablish a factory from a scratch. Once the decision is made and you have signed the contract, how will your project proceed? What are the next steps? Let’s take a look!
After the terms are agreed on and the contract has been signed, the project is handed over to the project managers. Sometimes you’ve met with the project manager already in sales negotiations.
“The project manager is in charge from the very beginning until the production is running and the warranty period is over. They are the person who has all the necessary information and who will help you with any possible questions throughout the project,” says Elematic’s Head of Project Management Riku Lehtonen. “By assigning a single point of contact from our team we aim to make the project management as simple as possible for you.”
Quite often the project is about increasing capacity, which may require building new space or adjusting the factory layout. How the project is done, and the exact requirements are clarified as the project proceeds.
Lehtonen estimates there are all in all 100 to 200 projects around the world handled every year in Elematic’s Project Department. All orders from software needs to larger equipment and full scale precast factory deliveries are also managed as projects. With collective experience gained from many countries and cultures, the project managers are skilled to solve problems and give advice on local matters. With experience comes also the ability to be flexible with any changes that may rise as the project proceeds.
“In practice, this means that we proceed as agreed but sometimes quick decisions are necessary during the project. For example, there may be adjustments to the list of equipment or components, and we look for the best possible solution for the project at hand, according to the need and budget. If there’s something that does not work as the project goes on, we suggest changes and try to find the best return to your investment. These changes are, of course, always discussed together with the project owner,” Lehtonen describes.
A strong foundation for tailored needs
Design and engineering start with a factory layout. The project engineering team designs the initial drawings based on the lay-out. Also, the plant conditions and energy sources are checked when making the initial drawings. Project engineering and designs are based on the specifications defined in the initial drawings.
After the initial drawings are approved, project engineering will continue. Every project is different and some of them require more tailoring than others.
“There are often limitations for using standard equipment, such as height of the plant or narrow spaces between pillars, and so on. We need to find the best possible solution within the given frame and answer the very specific needs there may be for the equipment,” Lehtonen explains.
The responsibility of designing the foundations and structural planning is on your side. But if you need support in designing the foundations according to local standards and materials, Elematic’s project department can help you in these matters as well.
“Some of the equipment can be designed right away. Large or complex projects proceed in phases and take a longer time to plan.”
Lehtonen notes that your project is in safe hands. A team of experts in equipment manufacturing, sourcing, and electricity, mechanics, automation and software designers all work under the same roof and communicate frequently.
“We have status meetings at least once a week for each ongoing project, involving all departments operating on the project.”
Delivery, documentation, training, and technical support
“We are very strict about keeping the schedule and it seems that we’ve succeeded as the customers have thanked us for punctuality,” Lehtonen says. Transportation procedures depend on many factors, but what is needed to organize the delivery is pretty simple: a delivery address and terms of delivery.
How is the product delivered? That depends on the equipment and how easy it is to unload. Usually the delivery takes place in containers. Large machinery is delivered in parts, by ship or by railway, and built and installed on the spot. The improved railway networks between Europe and Asia have speeded up the deliveries.
“Usually the equipment is installed by the factory personnel under our supervision,” Riku Lehtonen says. “Our team helps to define how many people and what kind of tools are needed in the installation phase.” In case there’s no personnel available, Elematic can also provide installation.
Training for the start-up of machinery and support during the warranty period are included in the project.
Once your factory is up and running and the warranty period is over, your factory will be supported by our customer service. Whenever you have problems with the equipment or production, you can contact our 24/7 HelpDesk.
As said, all projects are different. Is there anything the customer can do to ensure that the project goes smoothly?
“The process is quicker if there’s a designated project leader – a contact person – also assigned at the customer’s side. But there’s no need to worry – we support you at every phase,” says Lehtonen.
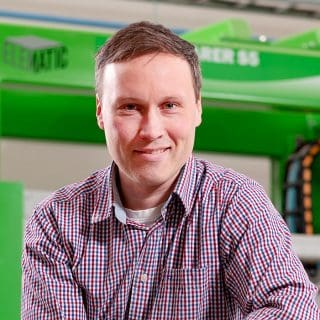
Riku Lehtonen
Roles in a project:
You:
- Confirm the plant location
- Provide factory layout
- Define production scope
- Make sure you have a skilled team and proper tools at site
- Ensure infrastructure schedule before line installations or machinery deliveries
- Assign a project manager from your side
Elematic:
- Provides initial drawings based on the data you provide
- Helps with structural planning and foundations if needed
- Provides layout design
- Designs equipment tailored to your needs
- Manages transportation and delivery according to contract
- Supervises the installation
- Helps with local authorities
ORDER OUR NEWSLETTER OR CONTACT US!
or