Reduce errors with digitalized quality control
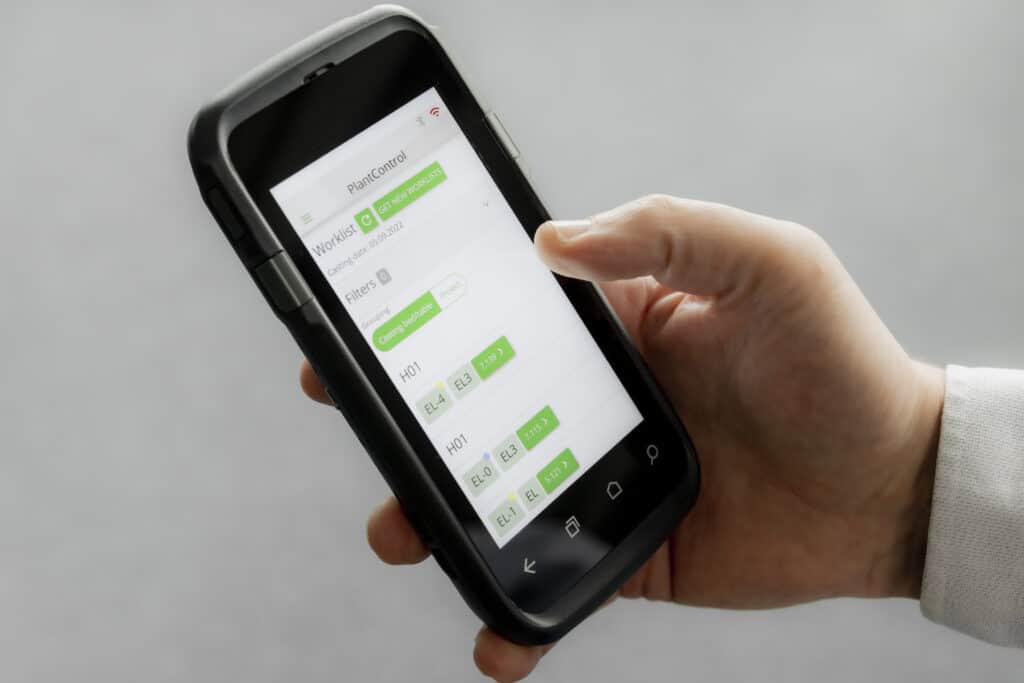
Elematic Plant Control Quality module turns mandatory checks into a continuous optimization process instead of a routine chore.
Quality control is a necessary but time-consuming task at precast wall factories. Finding quality information is difficult when you must look through hundreds of sheets in paper or pdf form.
The solution to this challenge is digitalizing the quality control process. This can be done easily by installing the right software.
The quality control module is part of the Elematic Plant Control precast software for wall production. The module can also be tailored for other types of precast concrete lines.
“The information management part of the process is automated. The quality engineers collect quality data with a tablet or smartphone, and the quality manager has a master view where he or she can control the process, look at deviations, understand how the process is proceeding, and make suggestions to improve the quality,” explains Jarkko Salmensivu, Director, Software Business Unit at Elematic.
According to Salmensivu, pilot users have found that the system is easy to use, and they have been very happy with the ready accessible digitalized information.
Go paperless and save time
How does the current quality control process go in your factory?
Typically, it starts with printing the quality checklist, then you go with a paper and pen to the product to fill in the form and take notes. Then you type the values into excel to calculate the tolerance levels. The ready document is then filed somewhere or scanned.
It can, however, be done much smarter, assures Salmensivu.
When digitalized, the quality control process could proceed as follows: The system calculates, based on frequency rules, which panels you are supposed to check today. You grab your tablet or smartphone and go to the first product and read the QR or barcode. After identifying the product, the system will fetch you a customized checklist.
“You have the option of pre-cast checking of the mold, measures, and materials in the mold, and then you can do post-checking, reviewing for example geometry, surfaces, and openings.”
Everything in one place
While you are feeding the system with information, it automatically calculates the key tolerances in the background based on the reference value. Goodbye, excel sheet!
If you need to check the drawings, they are only a click away. You can also take photos that will be saved with the panel data, a feature that eases the quality manager’s decision of rejection or approval.
“The quality engineer who does the check typically doesn’t decide whether to reject or not but just observes for irregularities. A description of a crack can be hard to understand. A photo makes it easier to perceive whether the panel can be repaired or should be rejected,” notes Salmensivu.
The last step is to save the checklist with comments and pictures, and you are ready to go on to the next panel. All data is stored in one single location in the database, so you can easily find and manage it.
Improve processes with fact-based decisions
In an average or large wall panel factory, you might have over 100 products that you need to check a day, meaning over 100 paper sheets a day or about 2000 a month!
“The minutes you save by simply not having to manage, scan, and store stacks of papers, are valuable work time,” Salmensivu points out. A paperless solution saves time later too, as you do not have to flip through folder after folder to find a specific piece of information.
In addition, digitalized quality control gives you the possibility to take a proactive approach; instead of just collecting the data that legislators and customers require, you can utilize it to improve your processes.
Thanks to its flexible reporting, the Plant Control quality module can easily find for example the five main issues that have caused correction work during the latest month.
“You can then improve the production processes in question and check next month again, how many similar faults you’ve had, and then determine next month’s top five,” Salmensivu suggests. “You can now focus on reducing quality errors to minimize fixing time.”
Up-to-date information, easily available at your fingertips, makes fact-based decision-making straightforward, Salmensivu notes.
“It might only take a short time to fix a process when you know what the problem is. Fixing the finished panels will take much longer.”
Share article
KEY FEATURES AND BENEFITS
- Saves time
- Paperless
- Can track and manage processes and progress
- Manager can follow the work of quality engineers in real-time
- Background calculations (e.g., frequency and tolerance)
- Information directly in digital format
- Possibility for checking pre- and post-casting phases
- All data saved in one easily searchable database
- Automatic, customizable checklist
- QR and barcode reader
- Easy access to drawings
- Photos saved with product data
- User interface fit for factory conditions with clear, big buttons
- Flexible reporting
- Also works with automatic cameras
MORE ABOUT PLANT CONTROL
ORDER OUR NEWSLETTER OR CONTACT US
or