It’s important to be realistic about concrete
Dr Karen Scrivener is a material chemist known for her groundbreaking work on cementitious materials, an area she has researched for over four decades. She heads the Laboratory of Construction Materials at Ecole Polytechnique Fédérale de Lausanne, where she is Full Professor.
We need to be realistic about the role that concrete plays in our lives and how we can mitigate its effects on the environment. One thing we do know is that because we use so much concrete – it’s about half of all the material we use – we also have a big opportunity to improve things. To put it in perspective, we manufacture about 4 billion tons of cement, which translates to about 10 times that amount in concrete. If we can make a few changes in the amount of CO2 emissions, for example, when you multiply that by the amount of material that we use, it can have a very substantial impact.
There has been a lot of discussion around what can be done to lower the impact of concrete. Some have proposed tweaking its carbonation capacity to enable it to capture more CO2. Although there is some margin there, it’s always going to be just a fairly modest proportion of the CO2 that’s being emitted. And there are going to be applications that cannot be used in all situations.
There have also been suggestions about making concrete blocks with bacteria. The fact is that doing this will not actually solve anything, because the calcium these bacteria use has to come from decarbonizing limestone in the same way used for the manufacture of cement. It might actually make it worse since you’d probably need bigger amounts of calcium. There is a tendency in media, especially, to focus on things that sound more innovative than they really are.
We have to keep in mind that 90 percent of concrete production happens in emerging or developing economies. We have to make sure that the solutions we come up with can really be used in the field. We also have to be practical. We have to think about how we can improve the whole chain.
We wrote a report a couple of years ago for the European Climate Foundation, where we estimated that just using technologies that are available today, we can lower emissions by up to 80 percent, by optimizing these different links in the chain.
The first level we need to work at is the level of cement. This is why we developed LC3, because it could lead to savings of between 30-40 percent. And then you look at the concrete level. We are very wasteful and we tend to put much more cement into concrete than we need to. We can save another 40-50 percent at that level. And then we look into the actual construction. Again, we use more concrete in structures than needed and the wastage rate can reach to about 50 percent or about twice what is actually needed. If you add all these levels up, you have very substantial reductions for this material.
We need to implement practical things while working on longer term solutions like carbon capture. But we have to realize the urgency of the situation. The concrete industry is very conscious about the issue of environmental degradation and it’s important to act now.
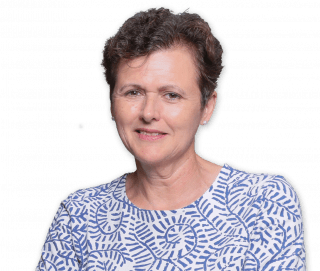
Dr. Karen Scrivener