Project done successfully
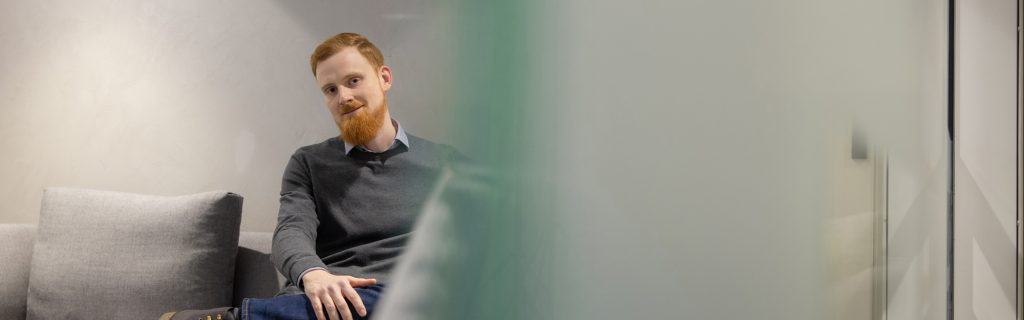
Are you planning to acquire a precast element production line? The experts at Elematic’s project engineering department are here to help you in all phases of the project. We listen to your wishes and work to provide the best solutions possible.
The procurement process for a precast production line begins with the quotation phase. First, we take a look at the customer’s production needs. You need to know what types of precast elements and how much will be produced. We will present you with products from Elematic’s portfolio to help you find the optimal type of production line. We will discuss the factory layout, technologies and software needed to achieve your production goals.
Once a deal has been made to acquire a line, it’s time for the Project Manager to jump in.
“In the internal kick-off meeting, Elematic’s design team, transport manager and procurement department discuss the delivery scope from Elematic’s perspective, taking into account any special requirements the customer might have. After the meeting, project delivery will be scheduled and divided into separate delivery batches.
We will go over any questions about the project, so we can find the best possible solutions together,” says Project Manager Thomas Richter.
In the initial design phase, the customer receives the first drawings of the design. After you have given your initial design approval, we switch to production and procurement. All changes will be agreed on in writing.
“Machine design starts with a mechanical design plan. Once approved, we move on to electrical and automation design. During the production phase, you (the customer) will already have a good understanding of what we are doing and what kind of equipment you are going to receive. We will inform you about the delivery timeframe. Our export department will handle the paperwork related to delivery,” Richter says.
When Elematic delivers entire production lines, we always agree on whether the Elematic team will handle the installation or if, as in most cases, we will send a supervisor to support the factory team with the installation activities.
“During startup, the operators will be trained to use the machines and how to change parts. The customer will also receive extensive documentation on the project, including manuals for the equipment they have purchased,” Richter promises.
After installation, the customer gives approval for the whole project. The warranty takes effect from here, with the Project Manager continuing as the first contact point until the end of this period. Once the warranty expires, the service department will take responsibility for the customer account.
”A successful project requires good communication between all parties involved, especially in the early stages of the project. We need to understand the needs and the situation in the factories. With every new project, I learn as much as possible about the scope of delivery so I am able to support the customer with quick answers. In case of more in-depth questions, I will discuss them with the design manager and engineering team, but I will always send a quick response to the customer to let them know where we are going,” Richter says.
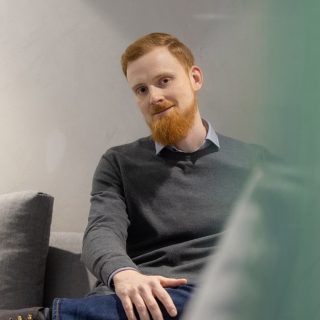
Thomas Richter, Project Manager
“Elematic has a lot of experience in the field and all our experts work under the same roof. We have developed state-of-the-art machinery to meet the growing demands of the industry. In cases of special deliveries, our expertise is a big advantage.”
Quotation
The quotation department designs the layout of the production line and makes a list of the products and prices in the offer. Detailed preliminary data is not always available, in which case the discussion will be conducted based on a basic production line model.
“When possible, we provide the layout designs also in 3D. This gives the customer an opportunity to walk inside the production hall on their computer or mobile device. Layout designs in 3D is something that only Elematic offers now; other manufacturers do not yet have this feature.”
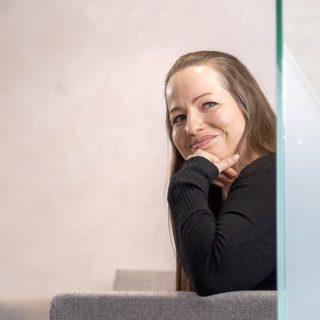
Sipriina Lahtinen, Sales Engineer
Design phase: Project engineering
For the most part, projects include standard Elematic equipment that is tailored to the customer’s needs. But often, deliveries also include some special equipment that requires agile product development from Elematic. For such tasks, a Project Engineer is appointed to lead the design project. The Project Engineer can be involved in the project from start to finish, from the preliminary assessment, to trial runs and testing.
“We have a lot of people working at Elematic with strong experience in the industry. I, myself, have been in Elematic for 14 years. The first time I dealt with Elematic’s machines was in 1998. Our customers usually have some special requirements, and it is one of my duties to make sure that these requirements are met.”
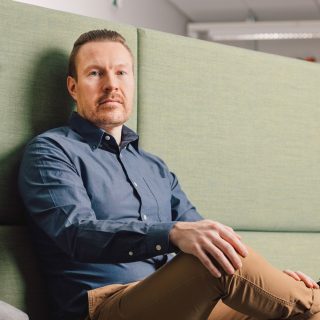
Markus Jantunen, Project Engineer
Machine design phase: Mechanical engineering
Mechanical engineering answers for initial data design and designing the steel structures in the equipment. Initial data design is the most interactive phase with the customer, and its purpose is to produce a layout and a process description approved by the customer.
Together, all the engineering teams are responsible for ensuring that the new production line meets all safety regulations and produces high-quality end products efficiently. For its part, mechanical design also ensures that the equipment is easy to use, safe, reliable, and easy to maintain. Mechanical design helps the customer find new features in the end products, such as different shapes and optimizations for hollow core slabs.
”Our engineering team will try to find the most suitable solution to solve challenges. We love being challenged. We are working in 3D-world, but our focus is on your factories.”
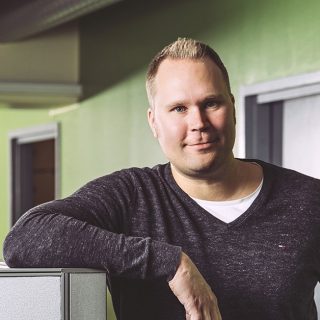
Janne Luotoharju, Head of Project Engineering / Head of the Mechanical engineering team
Machine design phase: Electrical engineering
Electrical engineering is carried out in close cooperation with mechanical and automation engineering. It is important for Elematic to get accurate information about the electrical network right from the start of the project because different voltages and frequencies are used around the world.
“We try to anticipate the spare parts needs by using the same components on different machines as much as possible. We use functional technology and available components so that the customer does not have to wait for spare parts for unreasonably long times.”
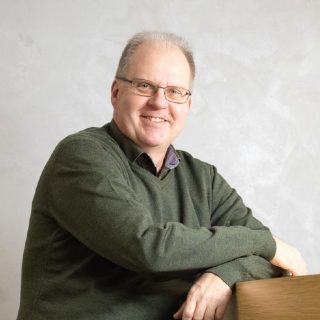
Taisto Aurola, Manager, Electrical Engineering
Machine design phase: Automation department
The Automation Engineer is responsible for the control system of the machine or the production line. The control system determines the level of automation that is needed to meet the customer’s requirements, based on the sales order. The automation department also tests the equipment before delivery, creates user instructions for user interfaces and participates in commissioning at the customer’s premises. The automation department reviews the operation of the production line together with the customer and ensures that the automation of the line meets the needs.
The production data required by the automated equipment comes from the customer, and its compatibility is checked at the earliest possible stage to ensure a smooth execution of the project.
“Our automation department has the experience to deliver what the customer needs. Each Automation Engineer has participated many, many times in commissioning and knows how the devices work in the factory environments.”
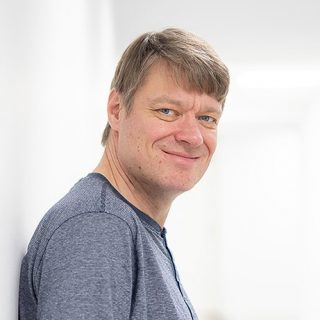
Teemu Mattila, Project Engineering Management / Automation, Head of Software Development and Deliveries
Documentation
After the design phase comes documentation which is done comprehensively from drawings and parts catalogues and delivered both in print and electronic form. All documents are translated into local languages in EU countries according to machinery directives.
“Our attitude in document localization is that it can be done in any language. Last year, we translated documents into 14 different languages.”
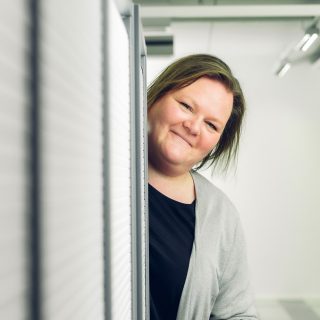
Elina Leiponen, Documentation Manager
Delivery
The logistics department closely monitors the schedule for completing the machines. It plans shipments, makes requests for quotations and orders transports. Pressure in meeting the schedule pressure is high, and timetables are always changing, so being able to anticipate problems is important.
“I have been working for 39 years at Elematic, in various positions, for example, as Project Manager. Experience helps you to anticipate things, and you quickly learn how different machines can be sent to a customer.”
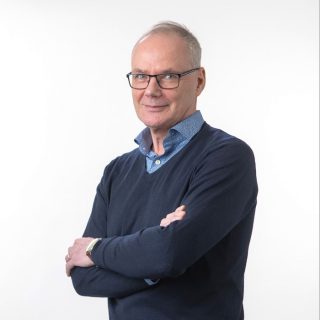
Timo Ahlfors, Logistics Manager