Pauli Beton is built on trust and respect
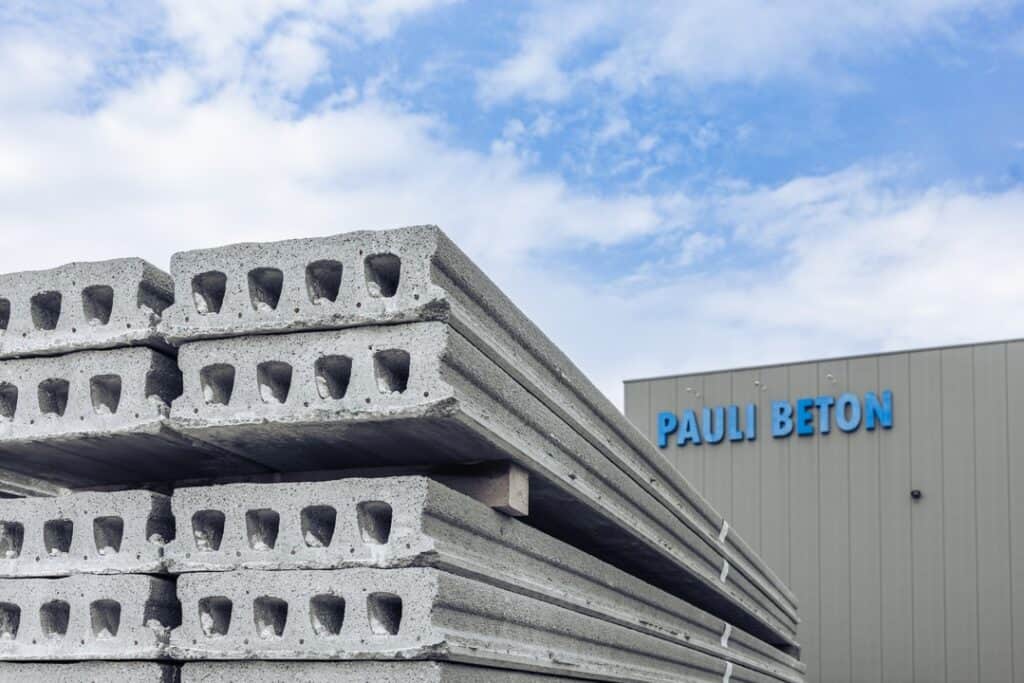
Belgian precast manufacturer Pauli Beton is a 100% family-owned company. Its success in the hollow core business comes down to a high degree of automation and a deep respect for team members, clients, and partners, says Manager-Owner Steven Pauli.
Pauli Beton, located in North Belgium is truly a family business.
“My sister is in Sales, my nephew is head of production, and another nephew is head of planning and engineering. I do the general administration,” explains Steven Pauli.
His father and uncles founded the company more than 60 years ago, and in 2003, the second generation took over. Today, Griet, Jean-Marie, Bart, and Steven Pauli share the management responsibilities equally.
The human factor
“Human values are very important to us. We don’t consider our clients as numbers; we know them by name. The same goes for the 30 people who work here. We are all humans who deserve to be treated with respect.”
In addition to respect and human values, Pauli Beton offers a total range of prestressed hollow core slabs and quick agile customer service to contractors and developers in Belgium, the Netherlands, and France.
In 2012, Pauli Beton started hollow core production from scratch. With help from Elematic, they managed to build a well-functioning factory that has served them since.
“We had no experience in hollow core prestressed slab production, but now, a good 10 years later, it has become a huge success,” says Pauli.
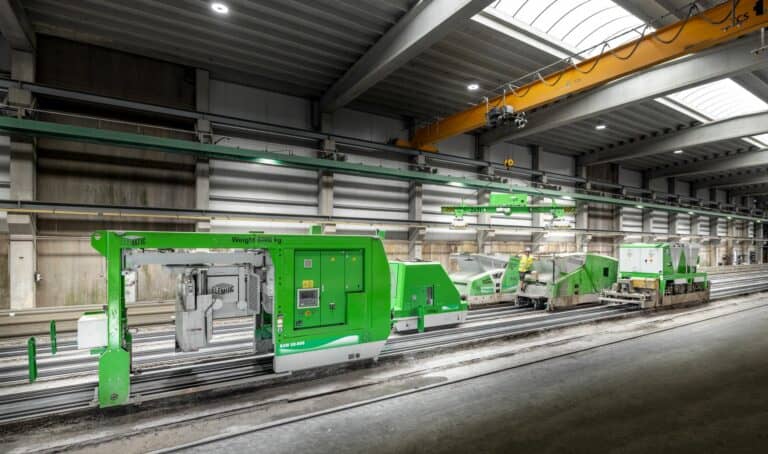
Automation is a must
In recent years, Pauli Beton has invested a lot in automated production equipment such as Extruder E9, Saw E9, and Plotter E9, and in the Plant Control Floor software suite. When labor is scarce, investing in modern, automated technology is the only way to go, notes Steven Pauli.
“Thanks to innovation and automation, we can still have a production of many thousands of square meters per year. Automation is necessary to survive in these difficult times.”
Choosing Elematic as the supplier of automated equipment was an easy decision.
“We’ve been very, very satisfied with their solutions during the last 10 years,” Pauli says, highlighting the continuous and good relationship with Elematic’s salespeople. “The contact with Sales is important because they are the first contact when you have an inquiry or need a new machine.”
“I want our suppliers to treat us as we treat our customers. We have a very good relationship with Elematic, and it is clear that we are not just a number in their database.”
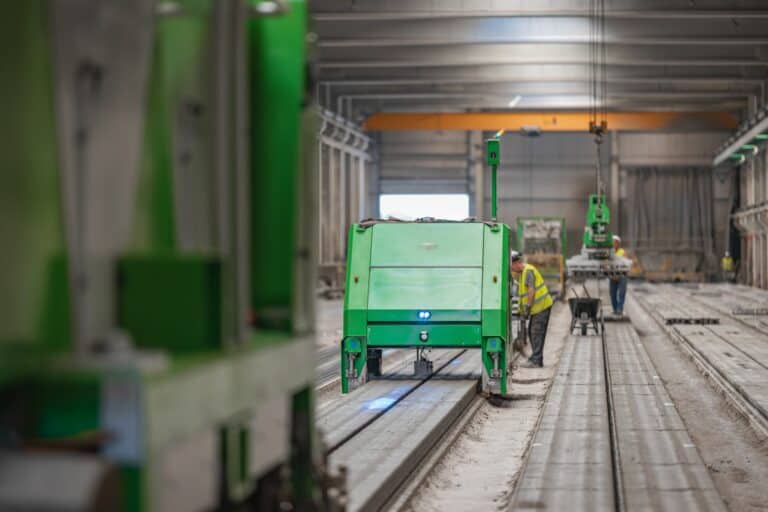
New plotter has doubled efficiency
When the Paulis bought the automated Plotter E9 two years ago, some of the team members were concerned that it would not work well enough. The operator was also reserved. But the fears turned out to be unfounded.
“The plotter operator cannot work any other way now,” says Pauli. “Nowadays, he is one with the machine that he takes care of and cleans nicely. He is fond of it and proud of the work he can do with the plotter.”
Steven Pauli is satisfied with the plotter too. The new plotter avoids so many mistakes that the efficiency has doubled, he says.
Quietly proud
The executive quartet and their employees have plenty to be positive about.
Despite high interest rates that might dampen the housing market, Steven Pauli believes that the Belgian building industry will remain stable. Especially hollow core slabs are in high demand.
“The hollow core slab is a sustainable product with a long life cycle, which is a benefit in this world where everybody needs to produce sustainable products,” he notes.
He is also proud of the way he and the three other Pauli owners work together to continue the family business into the future. Last, but not least, he is happy with the quality product that Pauli Beton delivers. Not long ago, he felt this at the airport in Liège.
“I was waiting for boarding, and I looked up at the ceiling and saw my slabs there. It filled me with joy that my slabs had been used in this huge building. Nobody knew, but I was proud.”
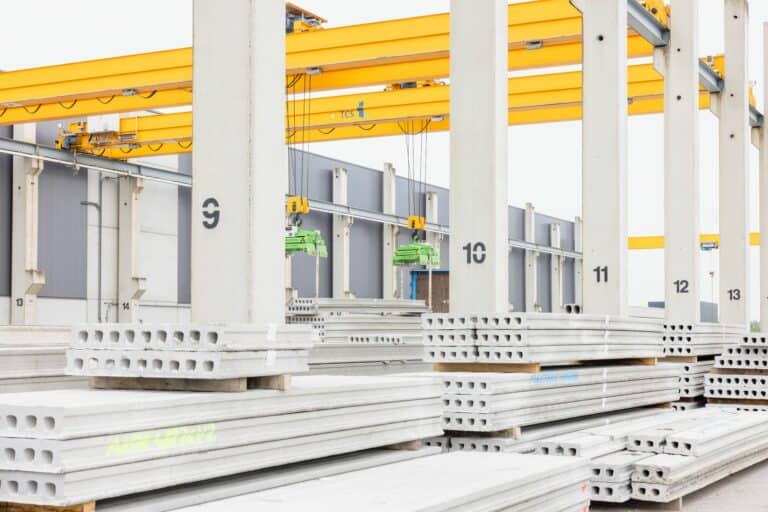
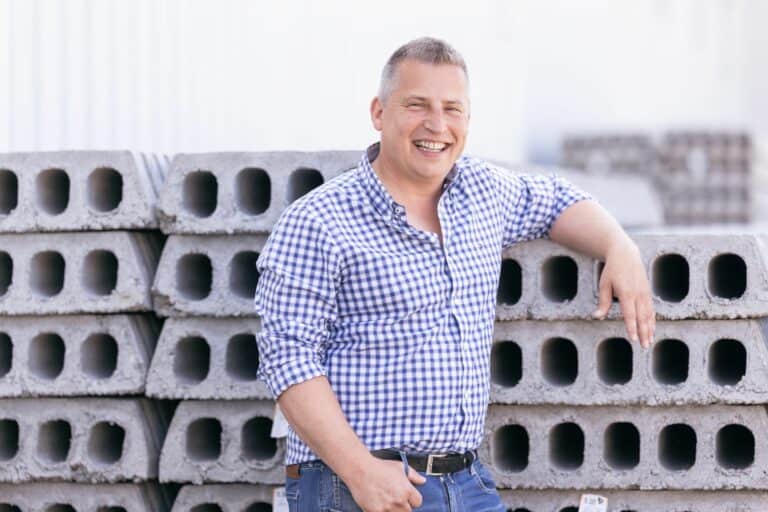
Cooperation from idea to ready slab
Pauli Beton and Elematic’s cooperation started in 2008 when now-retired Lothar Speate from Elematic GmbH and Steven Pauli met in Rotterdam.
This meeting marked the beginning of a respectful partnership between the two companies. Many, many square meters of hollow core slabs have been produced in Hoeselt since, and the story continues.
Everything started with the Slipformer, and today you can see Elematic’s automated extruder, saw, plotter, and other modern equipment in the factory. Digitalization has arrived.
“It makes us happy and proud to follow companies that we have supported in the investment phase and see how their production develops and becomes a success,” says Juhani Aittola, Managing Director of Elematic GmbH.
“When a customer needs support or has new ideas, we are happy to listen and use our knowledge to achieve the best results together. Pauli Beton is a very good example of this way of cooperating.”
Optimized slab production with Plant Control Floor
Recent automated hollow core investments at Pauli Beton include Extruder E9, Saw E9 and Plotter E9. The automated production is managed with Elematic Plant Control Floor.
“After we got Plant Control Floor, we have much less paperwork, and optimizing production has become easy,” says Peter Medaer, who is responsible for slab production and transportation at Pauli Beton.
Utilizing every inch of the bed to produce a maximum of slabs is his goal, but it can be challenging at times. With Plant Control it is, however, straightforward.
“The software is very user-friendly, and it has been easy to implement digital production planning. We cannot produce without it anymore!”
Around five people from Pauli Beton have been involved in the implementation process. Medaer is proud of how smoothly the system has been implemented in the whole factory.
“For the implementation, we’ve received very good support from Elematic. When there is something going on or we have a question, I’ll send an email and they’ll immediately answer me.”
A while ago, there was a problem with a machine, and Pauli Beton tried to fix it themselves, but it did not work. “Then I sent an email to Elematic. They told us what to do, and the problem was solved! Now, I’ve learned to send an email immediately,” Medaer smiles.
“The software is very user-friendly, and it has been easy to implement digital production planning. We cannot produce without it anymore!”
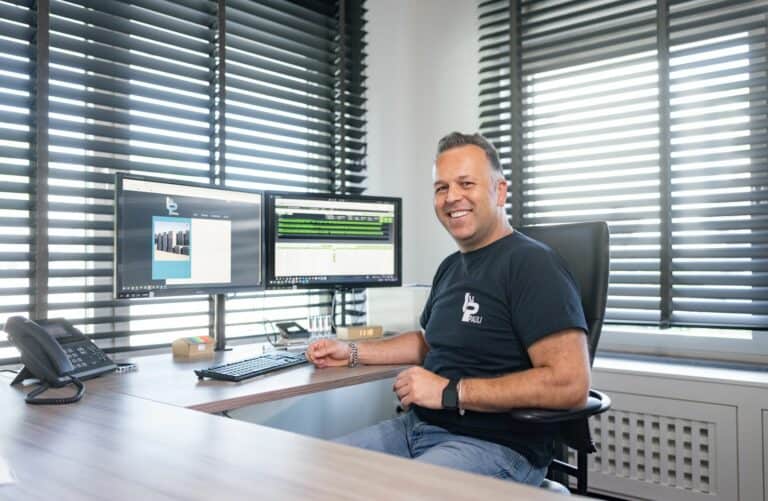
Products in use at Pauli Beton
Do you have questions? Please contact us!
or