New dimensions with sandwich panel façades
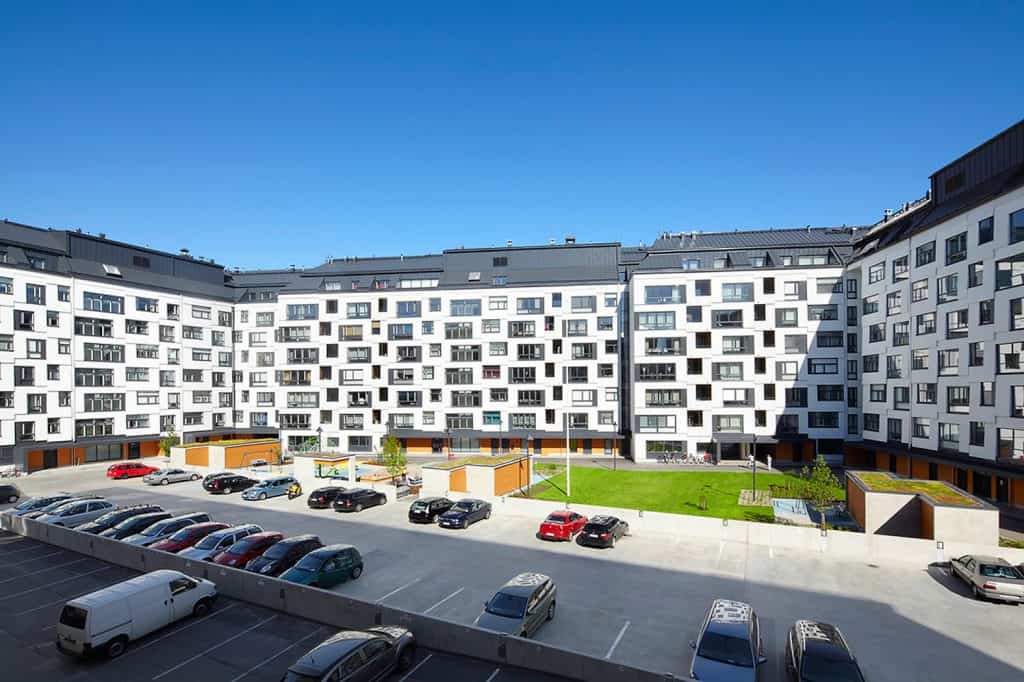
Sandwich panels offer a large variety of possibilities for different colors, textures, and exterior finishes. A beautiful façade doesn’t necessarily mean expensive techniques. Many surface treatment options are still somewhat unknown to architects and builders, says architect Maritta Koivisto from the Finnish Concrete Industry Association.
Buildings with sandwich panel façades can have very different looks, depending on the molds and materials used in the sandwich wall panel production, the colors of the walls, and the exterior finishes of the precast concrete panels. Ornamental themes and three-dimensional effects are gaining popularity in architecture, which has led to the rise of new, innovative precast production techniques.
“There is an incredible amount of exterior finishes to choose from, and architects or builders may not even know about all the different possibilities out there,” says architect SAFA* Maritta Koivisto, an expert in architectural consulting, design and conservation.
Koivisto is also Editor in Chief of the Finnish Betoni Magazine published by the Finnish Concrete Industry Association.
*The Finnish Association of Architects (SAFA) accepts members who have completed a degree in architecture at a Finnish university or, alternatively, a university degree in another country if the degree meets the requirements for architects specified in EU directive 20015/36 on the recognition of professional qualifications.
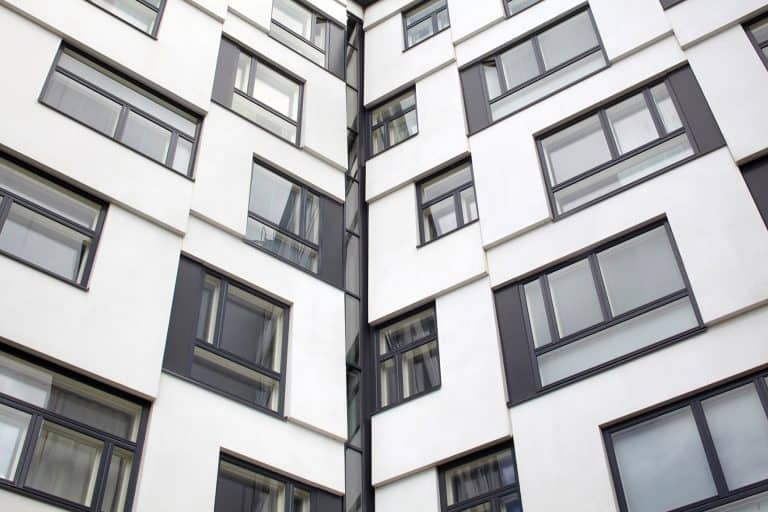
Choose the right materials and molds
Sandwich panels offer numerous possibilities for varying the appearance, color, texture, and architectural image of façades. The best option to use in any given project depends on the desired appearance.
One point to consider is the material used in the concrete mix. Is white or grey cement better, and what will the natural color or size of the stone aggregates be? These choices will determine the color and the smoothness (or unevenness) of the façade. Sandwich slabs can also be integrally colored, in which case color pigments are added to the mix.
The molds used in precast concrete wall production determine the look of the surface. Ordinary precast molds create straight surfaces, but more options are available with the help of extra equipment. Specialized molds can be used to create different shapes, patterns, and textures. The molds can be made of wood, steel, rubber, plastic or silicone, and their profiles are extremely varied. The surface structure of the chosen mold will also affect the perceived color of the wall. The molds can be unique and tailored for a specific purpose according to the architect’s vision.
Even intricate ornaments and sharp lace patterns are now possible by using fiber-reinforced concrete.
“3D surfaces have become more popular lately, and rubber molds are often used for this purpose, particularly in Central Europe. The patterns in the molds are designed using robotics and automation, and they can imitate lace, plank wood or brick walls, for example,” says Koivisto.
The choice of the rubber mold determines the shape of the surface, but what lays underneath the surface is equally important. The steel molds used in creating the precast walls must be of high quality, and they must be straight and dimensionally accurate — any curves or deflections in the molds will introduce the same flaws to the precast elements.
Coating or exterior finishing?
Sandwich wall panels can be coated or chemically treated in several ways. Plastering has been gaining more popularity during the past few years, especially in Scandinavia.
“It’s because we want to conceal the joints. With plastering, we can create a look that resembles traditional brick walls. The surface treatment is quite durable because the reinforced joint strips withstand thermal expansion well,” says Koivisto.
Precast elements can also be cladded with other materials such as prestigious natural stone, ceramic tiles, or brick tiles. Another option is to paint the walls with the desired colors.
The range of exterior finishes has grown lately, and a great variety are compatible with sandwich walls.
Fresh concrete is easy to process, and the final look of the façade can be affected by working on the surface when it is still malleable. An exposed-aggregate finish is created by spraying a chemical surface retarder onto the slab surface when the concrete is still fresh. The surface mortar is then removed by scrubbing or pressure washing. A beautiful and trendy version of this is graphic concrete that includes exposed aggregate surface and smooth surface.
Exterior finishing can be done to hardened concrete as well. One example of this is shot blasted concrete. The depth of the treatment can be light, intermediate or deep. Light shot blasting only removes the shine of the water-cement paste, whereas a deep treatment removes the paste almost entirely. In deep shot blast, the color and the appearance of the panels are mostly determined by the aggregates in the concrete.
Sandwich slabs can also be honed and polished, or they can be treated chemically or glazed to obtain a specific color such as blue, turquoise or umbra.
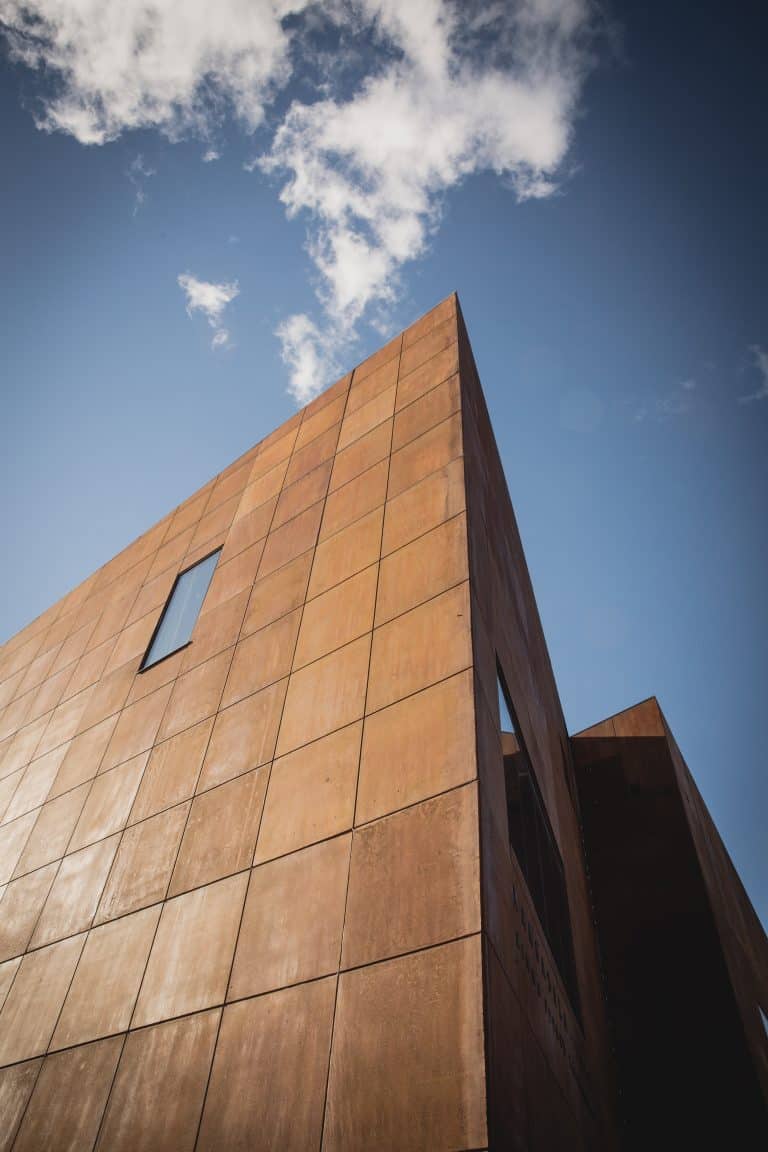
Inexpensive and diverse construction options
Because sandwich panels are factory-made, with windows and doors attached as they arrive at the building site, they are quick to install. Installation requires a minimum number of cranes and workers, and no scaffolding is needed. The size of the sandwich panels can be small or large, up to two stories.
“They reduce costs because less manual work and finishing treatments are needed on-site,” says Koivisto.
“The possibilities of different sandwich façades are endless. It is just a matter of knowing about the techniques and using them. A very interesting solution can be just as cost-effective as a basic version.”
As an example of this, Koivisto mentions the Kaanaankatu Housing project in Helsinki, Finland, where the variation of a few basic elements and different thicknesses of the precast elements have created a sense of harmony without the façade being boring.
“In the design phase, people tend to stick to tried and tested, familiar solutions and don’t look into more exciting or fresh options. But a job well planned is a job half done, and I believe that several successful examples worldwide will inspire architects and builders to try new things,” says Koivisto.
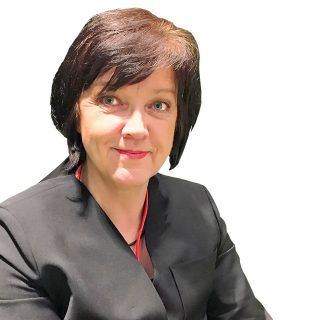
“It is sometimes forgotten that a wide array of techniques can be used side-by-side in just one building.”