How to avoid cracking in concrete slabs
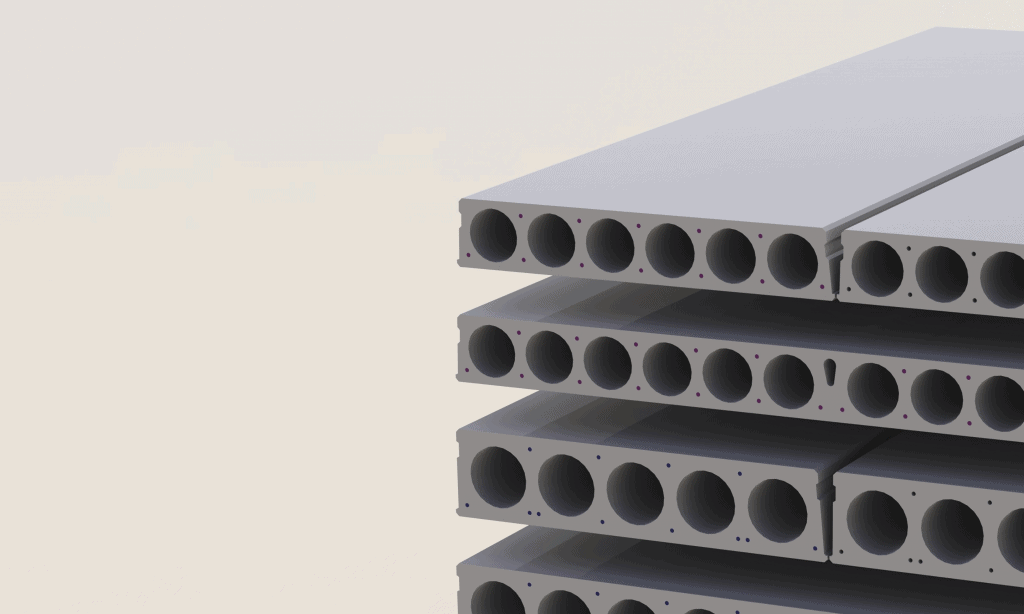
Cracking may occur in concrete for several reasons. Elematic Service Engineer Mikko Hellman explains the most common reasons for cracking and how to avoid them.
1. Release the strands in time and consider using fresh cuttings
Because concrete shrinks during the curing time, it is quite common to get transverse cracks in the slabs. The best way to avoid cracking is to release the strands as soon as the concrete has reached the required strength.
Another widely-used trick among precasters is to do one or two fresh cuttings per casted bed during the casting process. This means extra work and wastage, but fresh cuttings are worth these losses, when you consider that if even one slab is rejected because of cracks, the costs are much higher than doing fresh cuts.
2. Cover the slab, control the temperature
Covering the slab right after casting is important, as it prevents the slab from drying too quickly or unevenly.
You should also check that the temperature is not too high or uneven during the curing process. The recommended temperature at curing is between 45°C to 50°C, up to a maximum of 60°C. If the top and the bottom surfaces have different temperatures during the curing process, it may cause cracking.
Heating the casting bed is one way to optimize temperature. For example, here in the Middle East where I work, it is common to heat up the beds during the winter months.
I recommend using a tried and tested system for controlling the temperature and defining the optimal demolding time, such as Elematic Maturity Control System.
3. Avoid pre-stressing force that’s too high
Using pressure that’s too high during pre-stressing is another typical cause of cracking in slabs. Logically, the best solution is to keep the pre-stressing of the slabs on a moderate level. The standard is 3/8” strands for smaller slabs and ½” strands for bigger ones. Sometimes the precasters want to reach more loading capacity and stretch the strands to ½” for smaller slabs and 5/8” for bigger ones. Because pre-stressing pressure becomes too high compared to the strength of the concrete, this increases the risk of cracking.
The prestressing process reduces steel consumption. Because of this, in some areas, they attempt to achieve a maximum strength of the slab with minimum steel, leading to high tension. In Europe, the allowed prestressed force is limited to between 900–1100 Mpa.
A typical type of crack related to pre-stressing is a web crack. This can be solved by not using pre-stressing strands whose diameter is too big in relation to slab thickness.
At the maximum pre-stressing level, using upper strands may also prevent web cracking because they balance the tension in the slab.
4. Be careful during sawing
Cutting the slab is a critical working phase because during sawing, the slab bends and twists which can cause cracks at the webs.
A trick I’ve learned from precasters is to place counterweights on top of the slab during cutting time. A heavy counter weight, placed on the middle of the slab, helps to balance the slab and prevents the tension that may cause cracking.
Moreover, it is important to make sure that the concrete is hard enough before starting the sawing phase.
I also advise using the Elematic cutting saw program 2 or 3 when cutting high-stressed slabs.
5. Store with care
Incorrect storage is another possible cause of longitudinal cracking. Typically, the cracking occurs in the lowest slab of the bundle in storage. Making smaller storage bundle is the easiest way to tackle this challenge. How big the storage bundle should be depends on the thickness and the length of the slabs.
The storage space should have a flat solid floor.
6. Check the extruder settings
Any miscalculation in the slab design or incorrect extruder adjustments can sometimes cause problems.
If the top or the bottom of the hollow core slab core is too thin, the hollow core sleeves are out of the center line.
It is thus important to check the extruder settings regularly, to assure a good quality product and to avoid cracking and other problems.
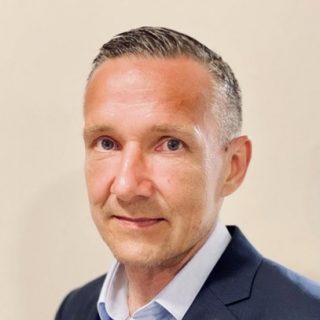
Elematic Service Engineer Mikko Hellman
The more stress we apply to the slab, the more common is the cracking.
A widely used trick among the precasters is to do one or two fresh cuttings per casted bed, during the casting process.