Figures in construction
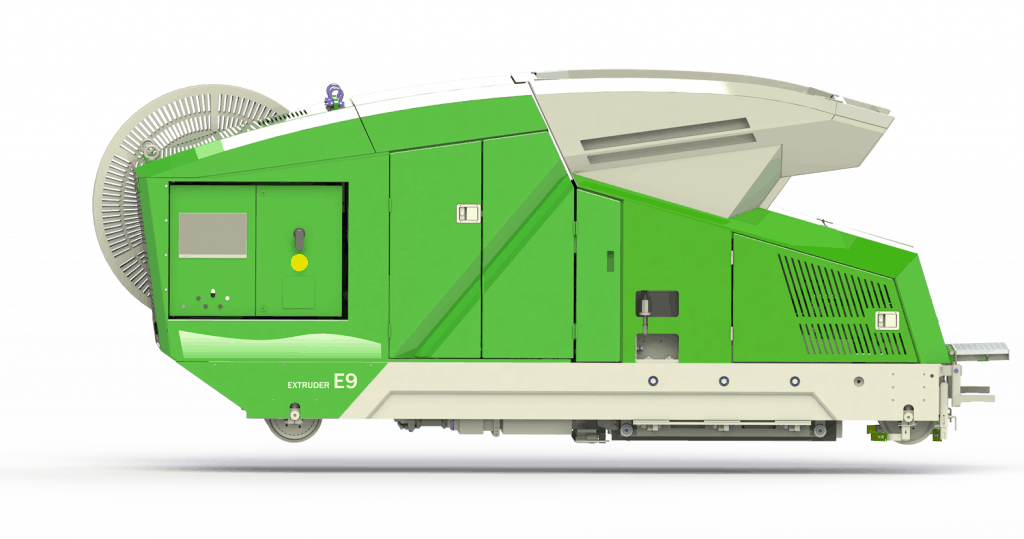
Up to 45 percent less concrete and 30 percent less pre-stressing steel is used in hollow core slab production, compared with a plain cast in situ reinforced slab.
–
In the average hollow core factory producing 300 000m2 annually, 5 400 tonnes of CO2-emissions can be saved by automated concrete recycling.
–
Using the Extruder E9 and Modifier E9 combo can save the average precast factory about EUR 135 000 annually.
–
In the EU-area alone, a decrease of CO2 emissions from concrete plants of 540 000 tonnes per year is possible to achieve by recycling concrete.
–
Conventional buildings use 150–200 kWh/m2/year of energy. By contrast, modern concrete buildings can be designed to use 50 kWh/m2/year or even less energy.
–
Concrete is 100 percent recyclable. Aggregates from demolished buildings can be used in unbound applications such as road base and even as aggregates for new concrete.
–
Scrapped precast from factories can be used to replace up to 5 percent of materials since scrap from production is high quality concrete.
–
The speed of construction is the key, because it also ends up to the costs. The interest rates for real estate projects in many developing countries are very high. E.g., in India and in real estate, the interest cost is between 18–20% annually. If the construction cycle can be reduced by 6 months, that is a direct saving of almost 10%.
–
Construction using precast is about 40 to 50 percent faster than casting in situ. It does cost about 5 to 6 percent more because of transportation and crane costs, but if you convert time in to cost, precast is cheaper.
–
Using copy spare and wear parts can cause unexpected costs. 15mm difference in the size of slab cores compared to the cross section in the drawings can lead to using 2 cubic meters more concrete on each cast bed compared to a cross section matching with the drawings. When casting four beds a day, 8 cubic meters of concrete is wasted every day. This means 48 cubic meters a week, 192 cubic meters a month, and almost 2,500 cubic meters every year. – 15mm difference in the size of slab cores compared to the cross section in the drawings can lead to almost 2,500 cubic meters of concrete wasted every year.
The extruder settings are also important.
With a 6mm oversized slab, 1 extra cubic meter of concrete is consumed per bed.
Roughly speaking, concrete / strands account for about 55% of the slab price and wear parts less than 1%. This means that it can actually be more expensive in the long run to save in spare and wear part purchases.
–
With the single stressing method, it takes approximately 2.5 hours for stressing 6 beds, while it takes only about 30 minutes with a bundle stressing machine, Stresser E9.
For example, if you save 1.5 meters of strands more per bed by bundle stressing: 1.5 meters x 6 strands x EUR 1 per meter x 6 beds x 250 days = EUR 13,500 per annum. This is the amount of money that would be wasted with the single stressing method.
If you aren’t currently using continuous strands for stressing, opting for the bundle stressing method and continuous strands can result in savings of 5 meters per strand. For example, if you save 4 meters of strands with continuous strands: 4 meters x 6 strands x EUR 1 per meter x 6 beds x 250 days = EUR 36,000 per annum.