Everything you need to ensure a smooth factory start-up
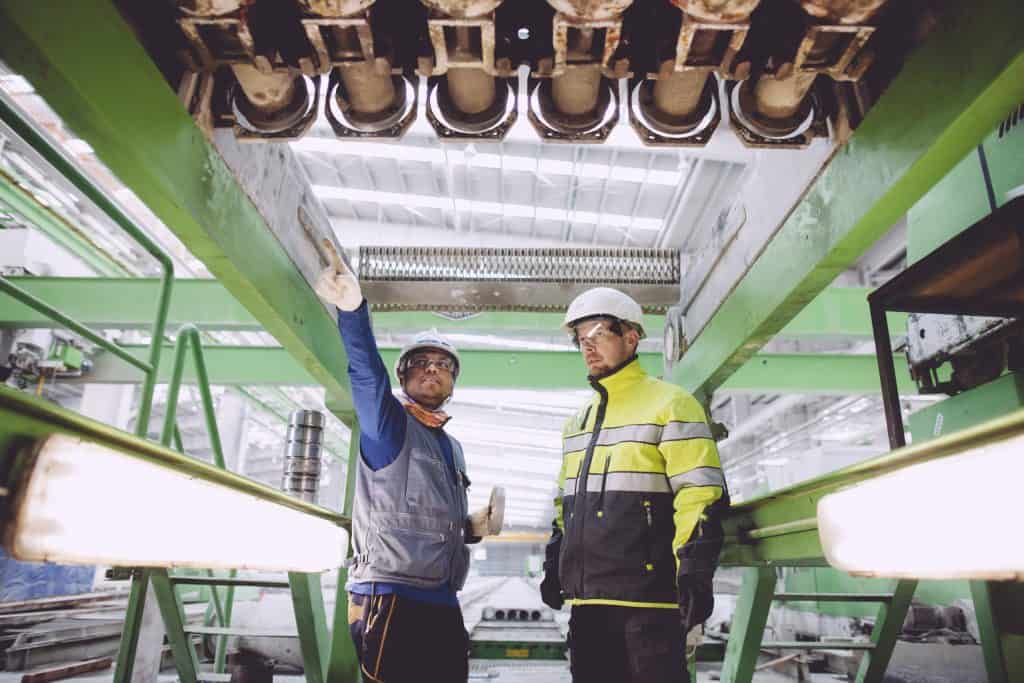
Now that the shiny new machines for your precast plant have been delivered, you might be tempted to start production right away. After all, the machines are there, you’ve bought tons of raw materials and you probably have customers waiting. But wait, there’s an important stage that you really shouldn’t skip over.
Between the two of them, Automation Engineer Janne Elomäki and System Engineer Heikki Mikkola have overseen hundreds of plant start-ups. They travel the world for most of the year, making sure that the the new factories, machines and software are in tiptop condition and ready for production.
“When the production line is almost finished, we run tests to make sure that everything works mechanically, that the electrical connections are fine and that the automation works,” Janne explains.
“We want to make sure not only that everything is running well, but that operators are trained before we make a test run with concrete. Otherwise, it could get really messy,” Heikki points out.
It might seem like an extra step, but the factory start-up is essential if you want to ensure smooth production. Think of the start-up phase then, as the general rehearsal, where you can work out last-minute problems before the curtains rise and your new factory performs before an audience. And fortunately, the skills you need for the start-up phase are things you’ve learned in kindergarten.
Here are some tips from Heikki and Janne.
We work better as a team.
Getting the precast factory up and running is the goal. We promise to do our best, but we also need you to cooperate with us and do your best, too. If we say that a setting still needs to be finetuned, we’re not trying to delay the project. We just want to make sure that the machinery and software you invested so much in are in top working condition. If we realise that the raw materials you’re working with are not optimal, please keep in mind that we’re not trying to add to your costs. Trust that we have your best interests in mind. Otherwise, it will be much harder to go through the start-up phase.
Let’s try to understand one another.
Communication can sometimes be challenging, but it’s important that we make the effort to understand one another. In cases where there’s no shared language, we rely on translators to communicate important technical information. This could sometimes be difficult if the translator does not have a technical background. We will do everything we can to avoid miscommunication, including showing, rather than just telling, how things are done.
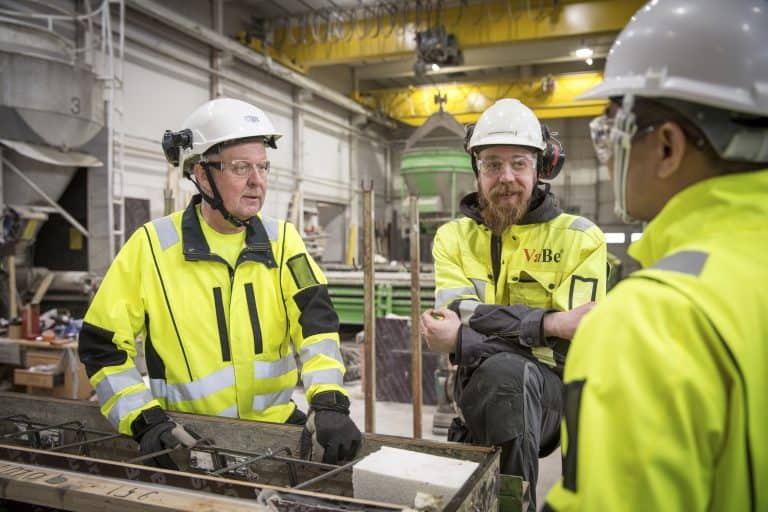
Attitude makes a big difference.
Especially in the case of new precast factories, the local crew may have only limited experience in the precast industry. If this is the case with you, please take advantage of our lengthy experience. Ask – and ask again – if you’re unsure before doing something. Be willing to listen to our suggestions. It could save you a lot of costly problems in the future.
Patience is key.
Precast plants are a big investment. We fully understand that you want to start production as soon as possible. However, please schedule some time for adjustments; there may be something that needs to be fixed in the machinery or tweaked in automation. Also, the shop floor crew will need time to learn how the plant works. Production cannot hit 100 percent on Day 1 but it will go up when the people learn to use the machinery and how to schedule the work.
Safety first.
Safety is our priority. At Elematic, we have incorporated many safety features into our machines. We rely on your crew to set up machines and to maintain safety standards. Trying to do things in a hurry can lead to accidents. And changing or overriding safety features can lead to severe, even fatal, accidents.
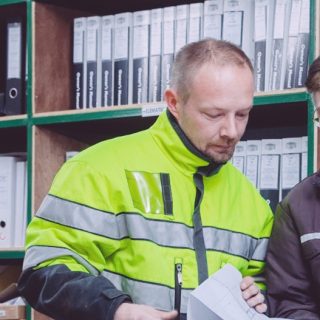
Janne Elomäki has worked on the start-up of the world’s biggest precast factory for Bismayah New City in Iraq. He travels to precast factories around the world for 150 days of the year. He says that the hardest assignments are those where there’s no common language. Thankfully, Google Translate is on hand; although, in the absence of internet connection, Janne finds that drawing with pen and paper could bridge the language gap. Janne enjoys knowing that he has helped customers, especially when he helps them with a problem that they’ve been struggling with for some time.
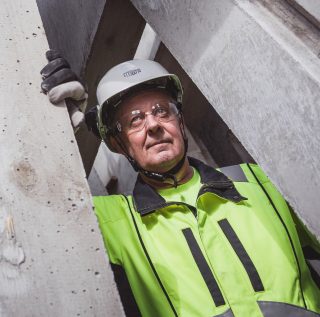
Heikki Mikkola is an Acotec production line specialist and spends about 200 days a year travelling, mostly in Asia. He looks forward to making sure that the machinery is running well, especially when new innovations or models are released, thus helping improve the end products. To Heikki, having happy customers makes his job enjoyable, which is why he tries to build trust through open communication. He’s happy to note that Acotec partition walls are gaining ground in Asia.
Do you have questions? Please, contact us!
or