Efficiency of hollow-core slab production improved with common sense and automation
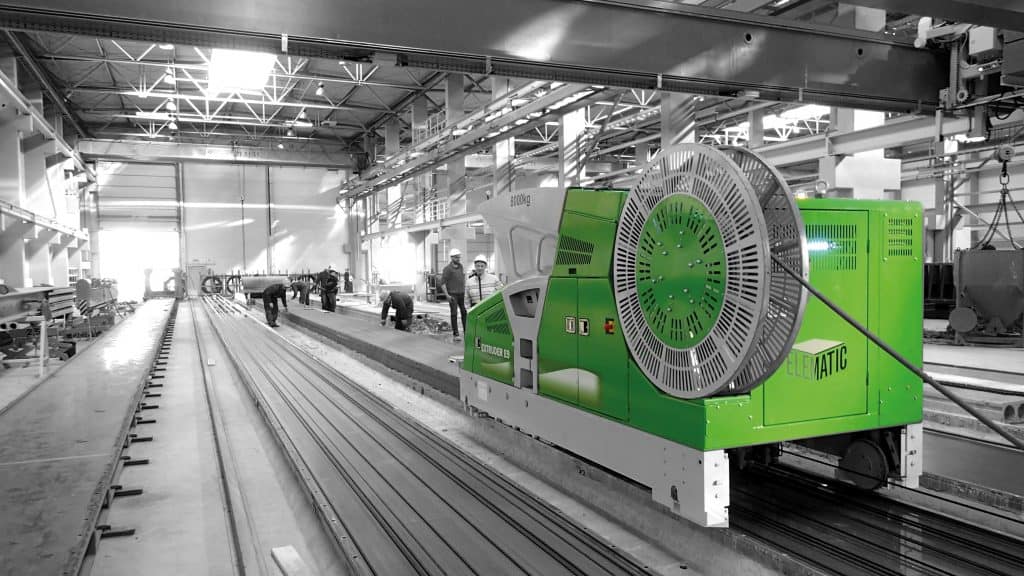
As an invention, the hollow-core slab is of mature age, but there are still many improvements that can be made to maximise production quality and efficiency. Whether it is an old production line or a new plant, the process can be improved by removing production-related bottlenecks and the material consumption can be cut down with advanced software and automation.
The use of concrete and the design of concrete structures has been established a long time ago, and the same regularities apply to both cast-in-situ and precast construction. Little by little, the technology behind admixtures has become more complex and the benefits of manufacturing precast construction elements in plants have become bigger. Batching is easy to carry out correctly in supervised plant conditions. However, it is still possible to reduce the quantity of cement when it is certain that the compaction of the concrete is done as smoothly as possible. This is possible with automation. The biggest effect on the compaction efficiency in hollow-core slab production is formed by the structure of the extruder and the compaction mechanism.
“Often concrete casting is a bottleneck for the efficiency of precast material production, especially hollow-core slabs. With the aid of advanced extruder technology, it is possible to increase both the efficiency and quality of the production. When automation is utilised in compaction, even structures with very closely inserted strands can be cast in such a smooth manner that concrete placement becomes all around even”, says Elematic’s Product Director, Floor Technologies Jani Eilola.
Eilola knows what he is talking about because he has seen a multitude of manufacturing methods for hollow-core slabs around the world. He states that the construction culture of a country has a large effect on how and what kind of hollow-core slabs are manufactured. If architectural individuality has been emphasised, as in modern-day Finland, it is not easy to reach big production runs. Operating in this kind of business environment accentuates the implementation of individual solutions in an efficient way.
“Another thing that leads away from mass production is the large quantity of issues related to building services engineering. Finland is a good example of increased building services engineering as well. When there are a lot of openings and different shapes, there are a lot of varying details, which become easier to implement the more efficiently automation and digitalisation are utilised”, says Eilola.
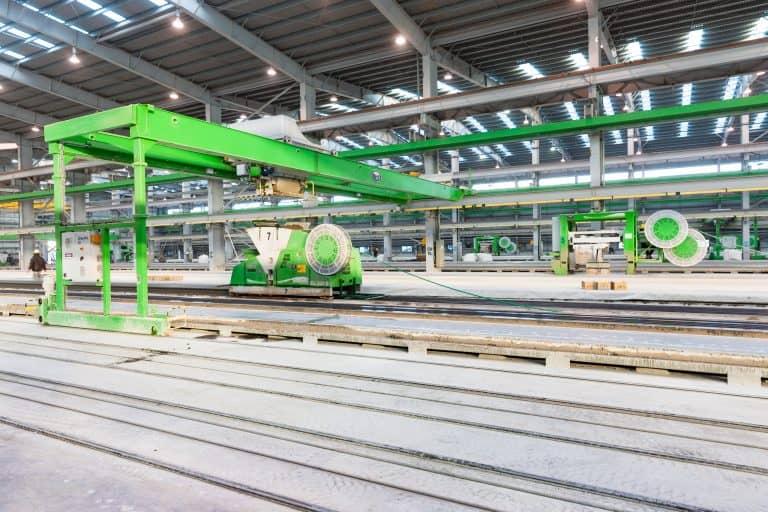
Minimising losses and defective products
The Internet of Things is starting to be an established fact in precast concrete element production as well. Of course, this has required that the designers and manufacturers of precast element production lines have realised how to apply this new technology.
“A definite advantage of the Internet of Things in precast element production is its capability to streamline the production process. Thanks to continuous data collection, it is possible to plan a production process which reserves a suitable amount of time for each work stage”, states Jani Eilola.
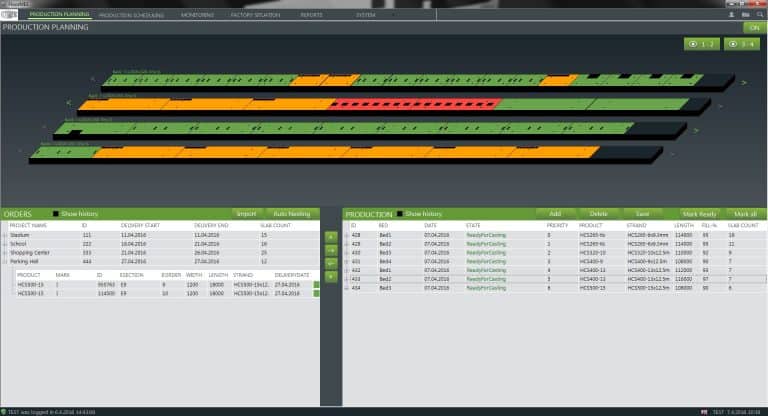
At least an equally big advantage in automation and digitalisation is that they optimise the use of raw materials. In any case, according to Eilola, the most essential factor is the compaction technology of the extruder, starting from the geometry of the screw and the used compaction movements.
“It is all about a smoother overall work process in the plant and that the material loss can be reduced even further with numerous small individual improvements”, says Eilola.
In addition, the length of the production line has an effect on the material loss. The longer the production line, the smaller is the loss that cannot be eliminated fully from the line ends even with automation.
Even older plants can be invigorated
When establishing a new hollow-core slab plant, the sales volume is first evaluated. The plant will be sized in such a manner that the utilisation rate is relatively high with the volume in question. It is up to the customer to choose how much room is reserved for expansion.
“Capacity differences in different production line options are fairly large. Among other things, the level of mechanisation and automation has an effect on what the best option is for the case in question. If the utilisation rate is high, the reliability of the machinery becomes more emphasised. Service is required but needed as little as possible when machines are manufactured to withstand wear and tear. A good example of this are feed screws that are subject to wearing during casting. We have developed a highly durable feed screw type”, remarks Jani Eilola.
If an old production line has machines still fit for use, there is no reason to replace them with new ones in every case for the sake of efficiency. It is still possible to improve the production process. First of all, a preventive policy should be taken towards the servicing of the machines. Second, concrete mixing can be improved with small investments.
Increasing the efficiency of internal logistics is also profitable. The layout of the production area can be inspected critically: Is everything placed optimally or could something be reorganised?
Jani Eilola provides one more simple suggestion for the improvement of old hollow-core slab production lines: lifting finished hollow-core slabs in bundles with clamps.
“Some time ago I gave a presentation of the production efficiency of hollow-core slabs in one of the conferences of our industry. I asked people to raise their hand if their plant used bundle lifting clamps. Only a few hands were raised. This was a bit surprising because bundle lifting clamps for hollow-core slabs have a very small cost compared to how much they increase overall efficiency”, he says.
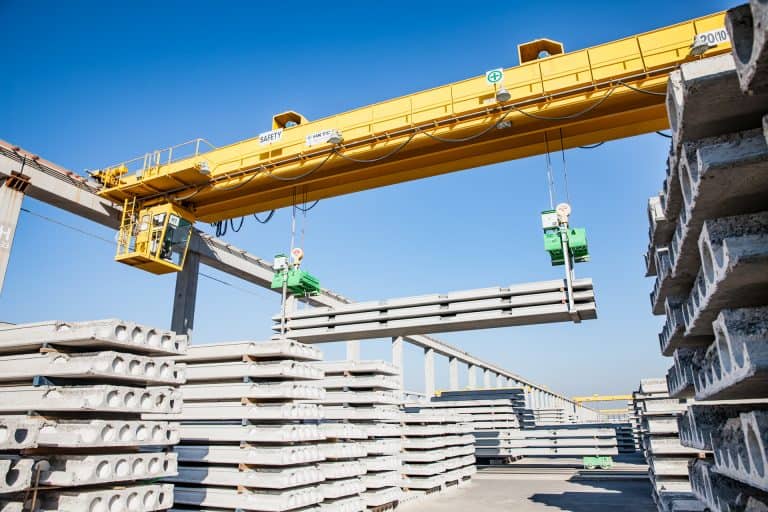
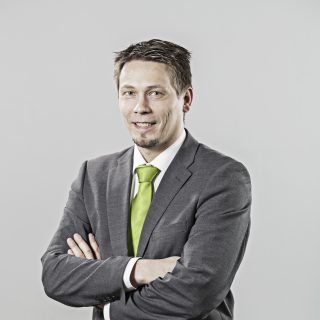
Jani Eilola
Product Director Floor Technologies at Elematic.
ORDER OUR NEWSLETTER OR CONTACT US!
or