Efficiency and transparency in the control of precast element production
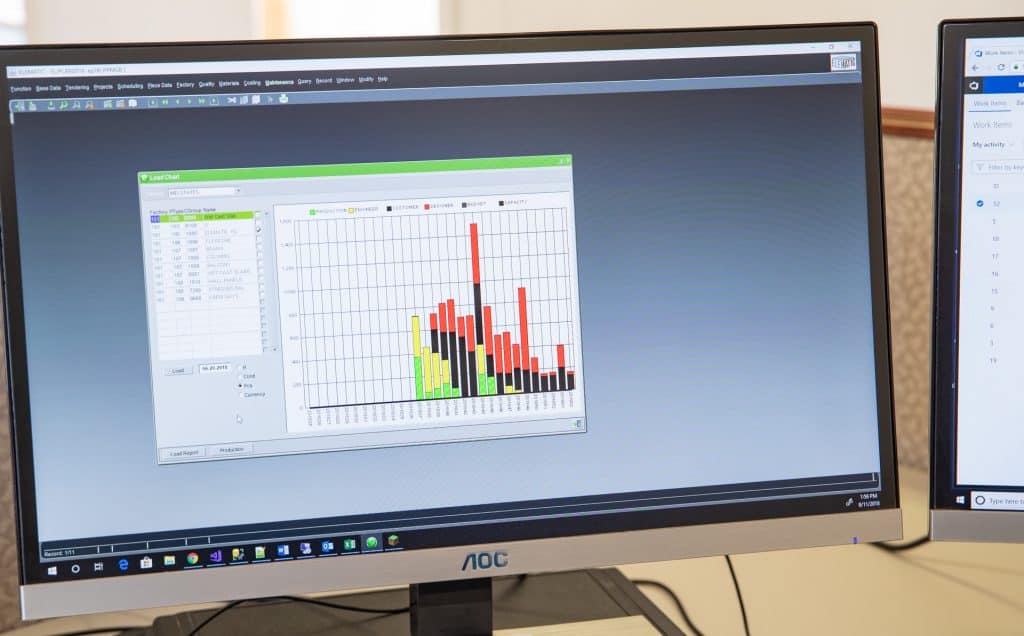
Most precast products are customized in line with the requirements of their intended applications, and therefore efficient precast production demands purpose-designed operation control systems. Repeated stacking, transport, and storage of finished precast products incurs significant costs and ties up personnel resources. Elematic ELiPLAN is an ERP system specifically developed for precast production purposes. It can handle the entire production process efficiently, starting from the factory’s needs and production planning, all the way to the delivery of goods.
Precast production is often highly customized and order-driven, requiring a great deal of flexibility from the order chain to allow the operation control system to function as efficiently as possible.
“Our operation control system permits us to keep costs under control easily through real-time monitoring of precast production. Management and control of production becomes easy when all the appropriate personnel have access to the information regarding a project’s progress. Savings are also achieved because purchases and production can be managed and controlled on the basis of received data”, explains precast production expert Heikki Kankkunen.
More accuracy for the optimization of production capacities and materials management
The system delivers clear savings through good production planning, covering the optimization of production capacities and materials management, as well as the tracking of precast products and minimization of transport.
Efficiency improvement starts already at the tender stage. After receiving the necessary information from the designer, the EliPLAN operations control system breaks down the products on the basis of material needs and work and production resources needed in the production processes. Thus, the system can be used to calculate exact material and resource needs for the project already when drawing up the tender.
“Previously, work and resource needs were assessed by the sales team at the moment of the order, using their own rough estimates, but now we can use both the measurements as well as material and dimensional information obtained from the clients’ 3D drawings. This information makes our tender calculation more accurate. As the system also helps us monitor factors such as personnel resources required by the factory’s production lines, mold stock, and material data, our cost control and management functions are more precise than ever before”, Kankkunen clarifies.
Thanks to EliPLAN, hollow-core manufacturing processes can be designed to utilize the entire area of the casting bed optimally, and material losses due to loop wastage can be minimized. The potential for savings from the minimization of loop wastage, enabled by good production planning, amounts to some €0.30 to 0.50/m2.
The capacity of cast beds used in the manufacture of wall elements often defines the maximum capacity of the factory and may therefore pose limits on the sales volumes.
“ELiPLAN allows us to optimize the use of casting beds so that two or even three elements can be produced on the same casting bed simultaneously. This, in turn, enables us to increase production volumes by a significant percentage, without the precast factory having to invest in a new production line”, reports Elematic ICT and Automation Product Director Jarkko Salmensivu.
Salmensivu points out that the system helps minimize expensive production shutdowns caused by material outages.
“Material flows can be planned in conjunction with production planning, so that the factory can always check the system to see which supplies are needed at various production stages and whether the correct ones are available when needed on the basis of the order book”, continues Salmensivu.
Thanks to the improved tracking provided by EliPLAN, material and product losses have been reduced by up to a third.
Availability of precast elements and minimization of transport
Every precast element produced at the factory can be tracked in real-time with ELiPLAN. Traceability not only aids in the control and management of production, but also brings about savings as time is not wasted searching for products in the warehouse. The user can easily find the exact location of the precast elements they are looking for in the system.
Since the sector typically involves frequent lifting and moving of heavy products, users will be happy to have the help of an operations control system able to optimize the order of lifts, storage, and transport. The minimization of unnecessary lifting, storage, and transport results in significant savings in terms of time, and thus the personnel resources previously allocated for these tasks can be put to better use.
“ELiPLAN helps us deliver the correct precast elements to work sites at the correct times, loaded in the order they will be used”, Salmensivu points out.
ELiPLAN shortens loading times and enables the driver to load the goods on his own, which makes it possible to schedule transport outside factory work times when necessary. ELiPLAN can also help to plan transport in order to avoid rush hours in the larger cities, thus ensuring better mileage and leading to savings of up to €1.70 /m2 in transport costs.