Conjuring up the finest grades
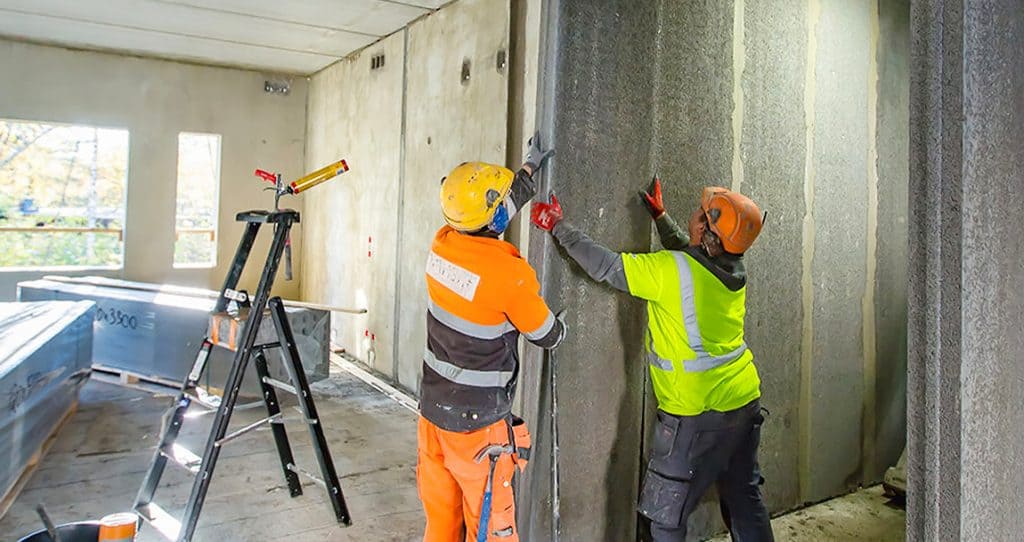
A new, innovative Atrex crushing mixer offers a solution for raw material procurement in Acotec non-load-bearing partition wall production. The new solution enables the use of lightweight aggregate up to grade 30 in Acotec panel production. The panel production thus does not require a selection of specific aggregate grades, which will result in considerable savings and simplify the production process, especially for producers in areas where fine-grained aggregate is not widely available.
Leca, a lightweight expanded clay aggregate used for cement mixes, is manufactured worldwide from natural materials. Leca products may, therefore, vary from country to country. Leca particles are generally larger than the size needed for the fine-grained cement mix used in Acotec production.
“Thanks to the new mixer, aggregate can be directly introduced to the Acotec production line. Otherwise, it would need crushing and screening before production,” explains Elematic’s Technical Director, Lassi Järvinen.
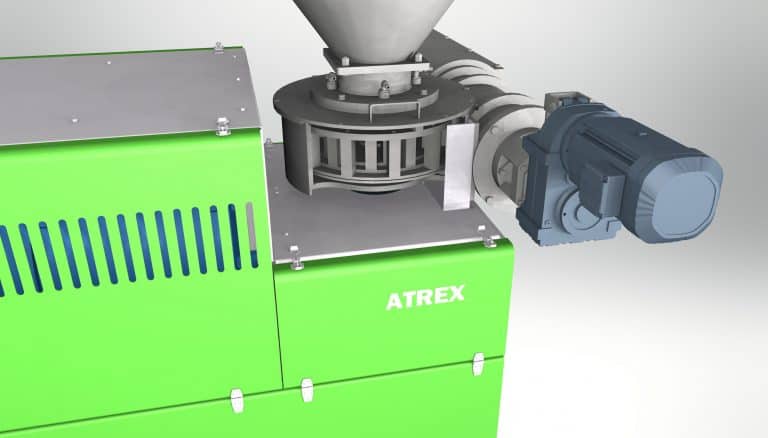
“Due to the continuous operation, cement feeding can be adjusted according to production requirements, which decreases the material loss.”
Well tested mixture
The development process behind the new solution kicked off in 2014 when Elematic’s Acotec production line was under development. The Acotec line had three new automation and capacity levels – SEMI, PRO and EDGE – to enable it to better address needs in different countries.
Elematic’s R&D team was familiar with the benefits of the ATREX technology, developed by a Finnish company called Megatrex, in many other industries.
Compared to the conventional batch mixer, the continuous operation of ATREX, combined with its simultaneous crushing and mixing properties, made it an interesting tool to improve raw material availability in Acotec production.
Soon after the initial meetings, collaboration began between Elematic and Megatrex, which are both based in Western Finland a short distance from each other, with test runs.
“First tests were made with different cement mixes to find the right rotor size. The test line was then set up on Megatrex’s premises. Based on the company’s extensive experience, tests were run with varying rotation speeds and mixture ratios,” says Jouni Sirkka, Director of Product Development at Elematic.
“Based on tests, a suitable mixture for Acotec production was identified. The continuous process has proved to produce aggregate with good quality, even better than with the traditional mixing methods.”
Innovative but proven technology
Despite being a new application in the precast industry, ATREX is a well-proven technology in many other industries that need continuous processes for grinding, mixing, crushing, and dispersing.
The technology has been developed in Finland since the early 1990s, originally for the forest industry.
“Proving the applicability of the technology for the forest industry processes was an important landmark for us in the late 1990s,” says Miika Partanen, Sales Manager at Megatrex. “The capability to run continuous operations in challenging plant conditions has been well tested, as well as the long-term strength of the rotors.”
Since the 2000s, the technology has been introduced in other sectors, such as mining and biotech.
“The well-tested and proven technology has been utilized to develop the ATREX unit for Acotec wall panel production. It has many similarities with other applications such as the pigment dispersion technology needed in the continuous slurrying process of the forest industry,” Partanen points out.
“The introduction of the new application with Elematic is proceeding with a moderate, well-planned scheme,” says Hannu Virtanen, CEO at Megatrex. “The less abrasive compositions will be produced before taking up the most sturdy materials.”
Based on effective rotors
The ATREX application has experienced a variety of development processes over the years. One of the remarkable innovations was the new gearbox that was launched in the 2000s, moving power transmission to a new level and improving energy efficiency substantially.
“The new gearbox enabled the effective rotors to run with one driving motor instead of two. The usability and serviceability of the machine improved, and 30 to 40 percent savings in energy consumption were achieved,” says Partanen.
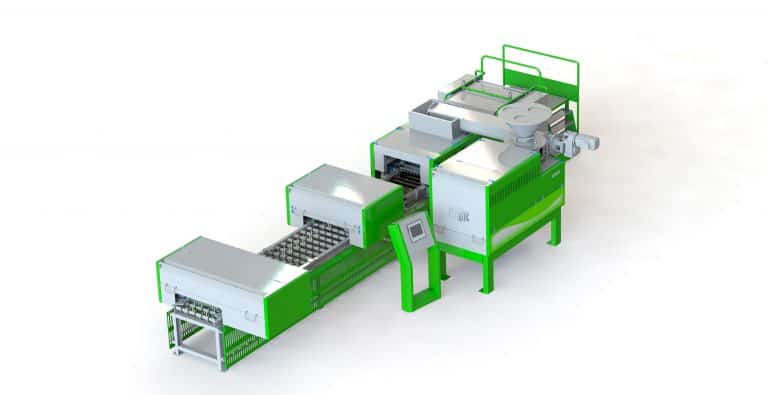
Production line for any investment size
Non-load-bearing Acotec precast partition wall panels have been manufactured around the world on Elematic Acotec production lines for almost 30 years.
The panels have various benefits, including excellent sound insulation, top-rate moisture resistance, and an easy installation method.
The production line, developed and manufactured by Elematic, featured three new automation and capacity levels last year.
The SEMI line, with a production capacity of 80m2per hour, is a simple line with practical combined restacker-handler and automated key functions. The PRO line offers a mid-level capacity of 100m2 per hour with automated functions for all main processes, whereas the fully-automatic Acotec EDGE offers a top-rate capacity of 120m2 per hour and requires only two operators.
Based on the different levels, the production line can be designed for demand at any size.
View: Elematic Acotec with Atrex continuous grinding mixer: https://youtu.be/G1iD6vNwq7g