The smartest way to build India
“The Maharashtra police housing project is about 5 million sqf residential development, comprising of about 60 towers and 5248 homes in all. We are building this entire development using Elematic precast equipment and methodology,” says Mr. Sandeep Bedi, Managing Director of IQB Private Limited.
IQB (Ingenious Quality Buildings Private Limited) is an innovative construction solution provider, with a specific focus on precast construction technology. They are India’s only end-to-end precast construction services provider, specializing in PMC, planning, production, logistics and installation services, and the principal contractor for B.E. Billimoria providing end to end precast services for MPMC. With a highly experienced and motivated team of over 100 precast professionals, IQB in on a mission introduce manufacturing efficiencies and culture in Indian civil construction sector.
In Sandeep Bedi’s opinion, precast is probably the smartest way to build buildings in India or building India itself as 90% of the building can be made in a controlled factory environment, free of weather dependencies and reduced labor dependencies.
Direct savings from speedup construction
Onsite precast plant minimized the crane requirement. The Maharashtra police housing project uses 4 tower cranes, each of them handling three buildings at a time.
“The ingenious part is that we are using one tower crane on three different buildings. The three buildings are at different points in the lifecycle: if we are installing walls in one building, the other building is at the stage for steels, the second needs services for the structural toping, and on the third building, we are in the process of laying the screed,” Mr. Sandeep Bedi explains. With the optimized way of working, enabled Sandeep Bedi and his team to get a floor cycle of 12 floors in 12 buildings in 12 days, basically a floor a day.
The speed of construction is the key, because it also ends up to the costs. The interest rates for real estate projects in many developing countries are very high. “The costs of money are staggering in India. In real estate, the interest cost is between 18-20% annually. So, If I can reduce the construction cycle by six months, that is a direct saving of almost 10%.” Mr. Bedi states.
Not just an equipment vendor
“The journey thus far has been extremely interesting, huge amount of learnings. And being with Elematic has been delightful. They bring in a wealth of experience, which is global, but they also have pretty much the maximum amount of information on Indian precast as an industry.”
“Elematic has held our hands and helped us beat every challenge. So, it’s been like Elematic is not a vendor from whom we’ve bought an equipment. They are actually a partner that holds our hand in every challenge that we are facing, be it a production challenge, an installation challenge, and even if we talk about manpower training.”
“I’m particularly proud of the partnership which we created with Elematic, with our team, clients, and the eventual users. Because of that partnership we’ve created a very high-quality product, which will eventually offer a lasting home cherished by families for a long time.” Mr. Sandeep Bedi concludes.
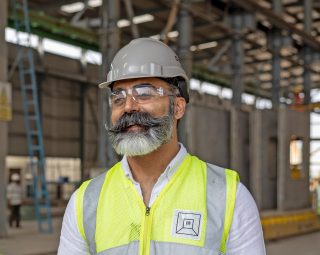
Sandeep Bedi