BIM and precast. What’s new?
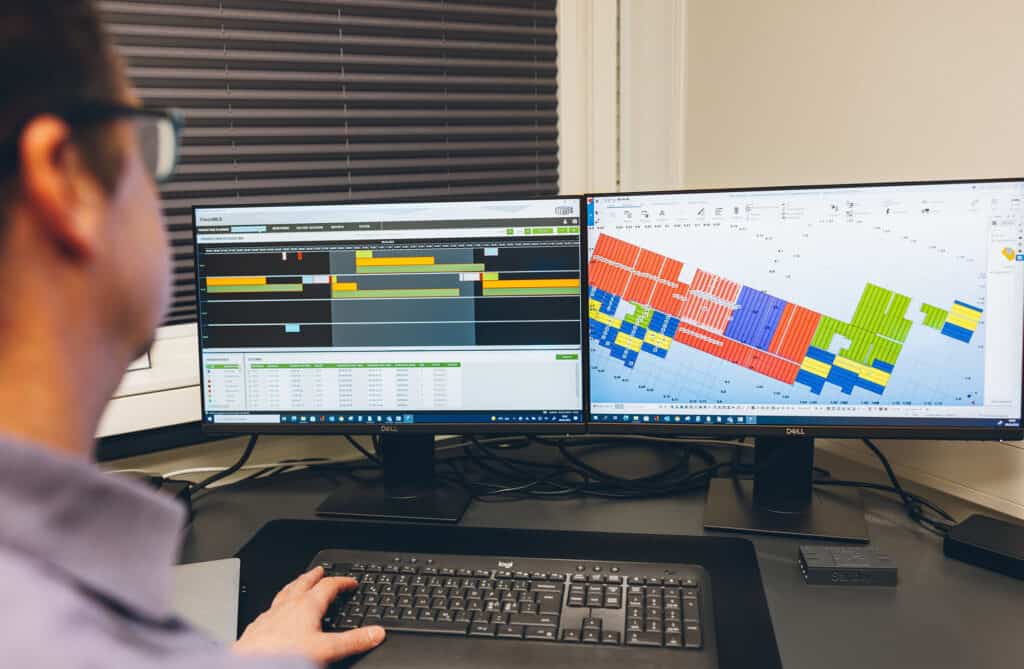
Building Information Modelling (BIM) is already widely used, but the term BIM has also many different meanings to it.
Globally, BIM is often used to explain the process of different design disciplines working together in order to avoid mistakes by combining the models to check for clashes and coordination.
But when looking beyond the design work and from the precast industry perspective, the possibilities offered by BIM are vast.
The idea is to model a virtual building (1:1) with each element containing all the details and reinforcements. While the model is constantly being developed during the project, it can store all relevant data, from structural information to precast production, scheduling, costs and logistics.
“The model data can be constantly updated, used directly with model applications or exported and used with third-party applications, but information can be also brought back from third-party applications to the model for reviewing, checking and coordination – depending on what’s needed,” says Business Development Manager Tero Kautto from Trimble Solutions, provider of Tekla Structures BIM modelling software.
There is still a lot of unrealised potential when expanding model usage from design and detailing work to cover the whole process. For example, it is easy and fast to compare alternative precast concepts at the beginning of the project in order to find the most cost-efficient and constructible solution. And after the detailing is made, there are a multitude of benefits for precast production, logistics and at the construction site.
“The tools are capable of doing many things, but the people must first apply these new processes,” Kautto says.
Large-scale construction projects such as the New Children’s Hospital or Tripla, both in Helsinki, Finland, are examples of the thorough use of the BIM model. Kautto emphasises that the process should be similar in all projects, big or small, not only in more demanding ones.

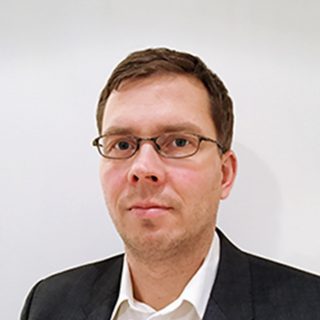
Tero Kautto
“The model data can be constantly updated, used directly with model applications or exported and used with third-party applications, but information can be also brought back from third-party applications to the model for reviewing, checking and coordination – depending on what’s needed.”
Focus on constructability
Beyond Tekla Structures, Trimble also offers Tekla Model Sharing and Trimble Connect that enables all parties to work using a model-based workflow to update the data continuously.
“Trimble Connect is a cloud server model that makes the data available for everyone. Our goal is to make this work process more common and involve all disciplines in the process,” Kautto explains.
Trimble Connect is easily accessible and the users can search and add information. For example, the installation dates of the precast elements can be added directly to the model instead of sending file attachments via emails. This way, everybody gets the information simultaneously.
“The most important thing is that the information is shared among all the necessary parties,” he says. Trimble Status Sharing is an example where data flows seamlessly and instantly between different platforms (Tekla & Trimble Connect) enabling everybody to follow the progress of the project.
In the construction industry, there is a lot of talk about automation. Kautto says that the focus is in constructibility – the model needs to be created as elements are produced in reality. This enables information to be exported directly to automated processes such as shuttering and mesh welding.
Optimising processes
Tekla Structures offers tools for precast process planning and project progress follow-up; for example, the erection sequence, production and logistics can be defined and followed from the model.
The construction site can also be laser-scanned and the point cloud can be brought to Tekla structures to compare the model with the actual conditions. This enables last-minute changes to elements before casting. But if something unexpected should happen at the site, the site manager can easily check the element status from the BIM model to find elements that are casted and ready for delivery to minimise waiting time and delays in erection.
Tekla can also help to define the optimal use of transportation – element placement can be planned to optimise use of transportation rack and erection order, this way the installation is as swift as possible. If the distance between the precast plant and the site is long, planning logistics efficiently saves time and money.
”If the capacity of a truck is 20 tons and the elements weigh over 10 tons per piece, the trucks are not optimally loaded. This can be optimised with production and logistics planning.”
”Big steps are taken constantly. I am convinced that when people get more familiar with purpose-build tools that are easy to use, the possibilities of BIM usage will be realised better.
Elematic Plant Control production operations management software suite is designed to work smoothly with Tekla solutions.
Elematic also offers BIM services including 3D visualizations and modelling or clash detection and coordination of your project. Services for construction management, scanning to BIM, energy simulations and virtual/augmented reality are also available.