Molin Concrete: “Beautiful slabs at a phenomenal speed”
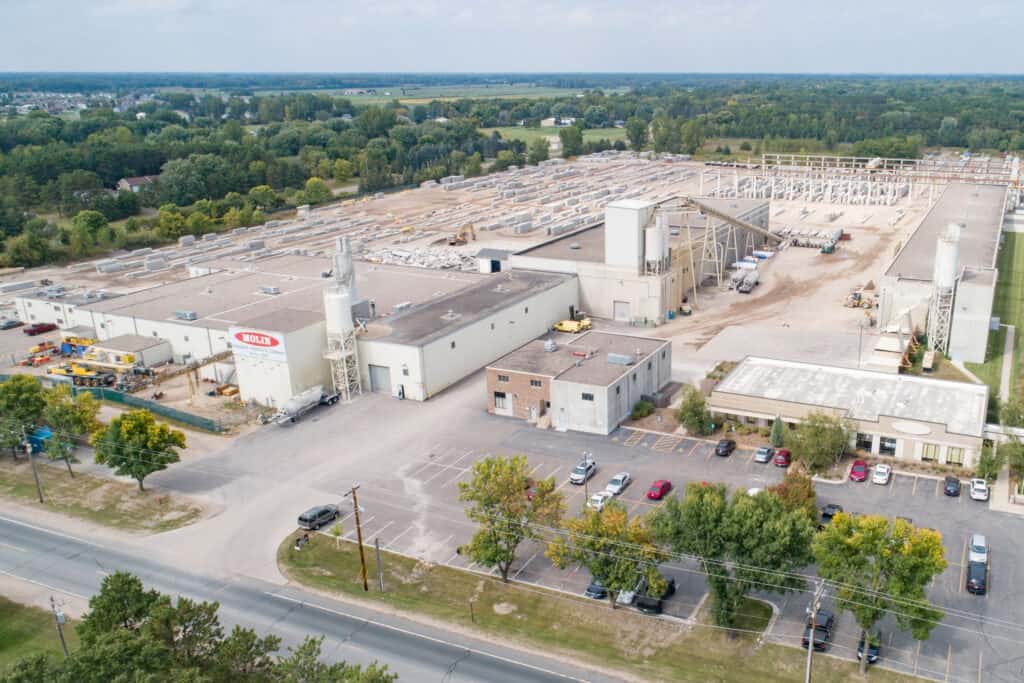
Since Molin Concrete Products took the new Elematic Extruder E9 into use in October, the production speed has soared. Molin staff praises the interface for being user-friendly, and the hollow core slabs produced by the machine for their beauty.
On October 1st, 2021, Molin’s precast facility in Lino Lakes, Minnesota, was upgraded with new Extruder E9 machine, producing 12-inch slabs.
“We have two different profiles: 12” light and 12” heavy,” Director of Manufacturing Mike Rufenacht explains.
Founded in 1897, Molin Concrete Products designs, manufactures and installs precast and prestressed concrete components. Molin serves as a single source for the complete precast/prestressed building system throughout the 7-state Midwest region of the US.
High production speed
“By using the new E9, we’ve been able to go from six beds of material up to eight, so we’re actually stripping two additional beds,” Mike Rufenacht says, adding that the slabs produced by the new Elematic machine are beautiful.
Ben Lisowe, maintenance supervisor at the Lino Lakes facility, describes the new machines as “miles ahead of where we were.”
Lisowe has overseen maintenance for about six years and has been working on Elematic equipment for almost 20.
He depicts the evolution from the labour intensive 900 series machines, running around 2-3 ft/min over the old P7 models with 4-5 ft/min, to the E9 that on an average day can run 7-8 ft/min of normal casting.
“We have run it up around 11 ft/min, but we run into process constraints of getting concrete to the machine fast enough without the machine stopping,” Lisowe explains.
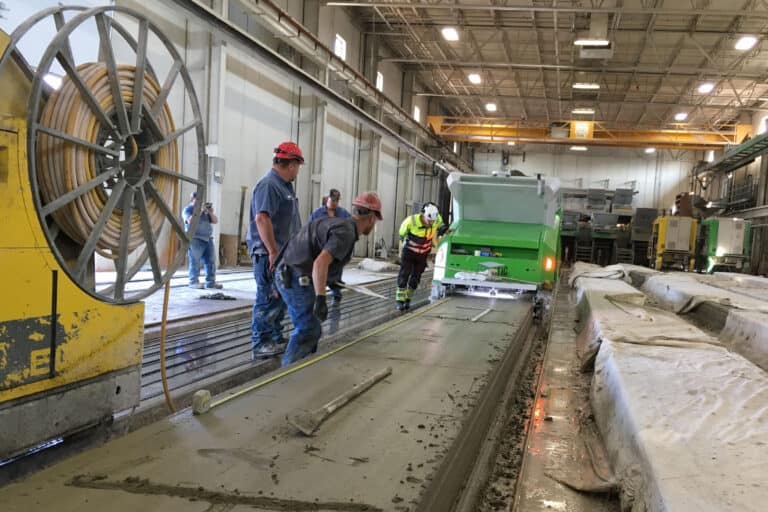
Let others enjoy this article too
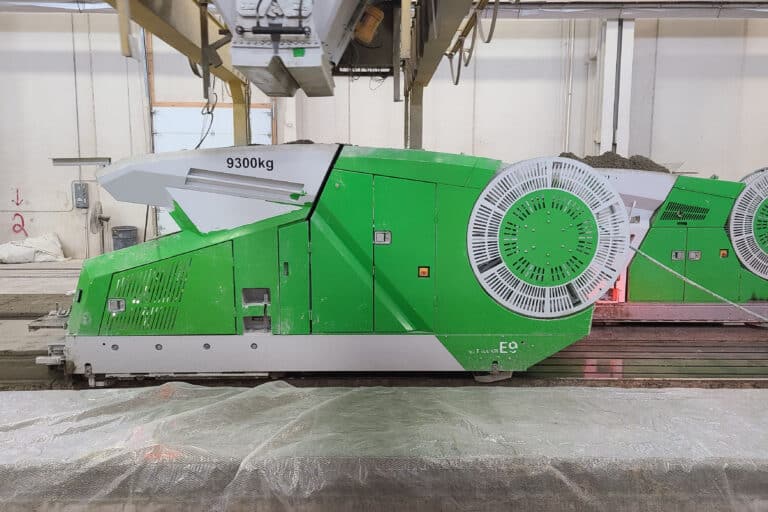
Automatic troubleshooting
In addition to production speed and the quality of the slabs, different members of the Molin Concrete Production team all highlight the E9 user interface.
“The software on the machine is extremely user-friendly. If there is any issue, the machine will troubleshoot the issue for you. It will tell you what is wrong, and it makes it quick and easy to get back up and running,” says Mike Bruen, production supervisor at Molin.
From a maintenance point-of-view, the automatic troubleshooting is a great feature, says Ben Lisowe.
“If, for example, a door is left open, it tells you on the interface screen, quickly and easily, where to go and what to check. It makes it very easy for the maintenance or production site; if they check something, and the door didn’t shut all the way, it’s very quick to get production up and running again.”
The possibility of changing the settings, while the machine is casting is also worth mentioning, Lisowe adds. “You don’t have to pause production to make an adjustment on the machine.”
Maintenance made easy
So far, the Extruder E9 at the Molin facility has purred like a kitten, and no repair work has been required. Nevertheless, with his 20 years of experience with Elematic equipment, Ben Lisowe already sees many advantages to the way the machinery is built.
“When the time comes that we have to do repairs on it, it’s going to be much easier to get access to all the parts and replace them,” he mentions.
Several features are, in Lisowe’s opinion, worth highlighting.
The way the side plates are designed makes them easy to adjust, and the fact that the underside of the machine is now a multi-piece unit instead of a one large plate, also makes replacing of parts much easier.
“Now, you only have to replace the part that is actually worn out instead of the entire assembly,” Lisowe rejoices, before he goes on to talk about the new strand guide design.
He calls the design, including the electronic adjustment for the strand guides, “phenomenal.”
“On the old machines, if stuff started wearing out, you had the possibility of dropping a strand, and then you’d have slab issues and rejections. The new design for the strand guides does not allow you to drop a strand. It supports all of them at the same time, at the same height,” he explains.
“The production guys can drive up to it, hook it up, and it automatically sets it to the exact height every single time. There are no hydraulic hoses that could break, or parts that can really wear out, because it supports the strand at such a large area.”
Also, the E9 levelling beams are significantly better, he adds.
Great equipment = happy team
With its variable speed drives, the E9 also has another great advantage: It’s quiet.
“The guys used to have earplugs and shout to each other. Now, you can carry a standard conversation next to it, and the machine can start and stop, and you’ll barely know that it’s running,” Ben Lisowe says.
The whole Molin team is happy with its new Elematic purchase, Director of Manufacturing Mike Rufenacht says. He would not hesitate to recommend the E9 to other precast manufacturers.
“It’s not just about whether I’m happy with it. People who are using it are pretty darn happy with it as well.”
RELATED
ORDER OUR NEWSLETTER OR CONTACT US!
or