Automation in hollow core production reduces costs and makes operations more accurate
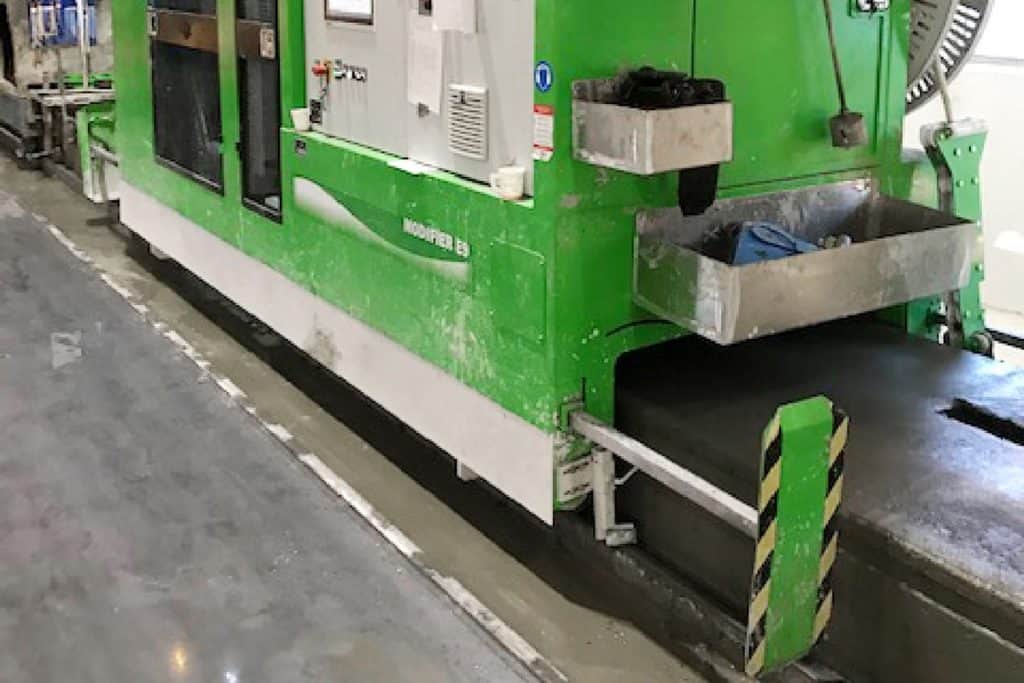
Automation reduces labor costs and heavy manual work. An example is the Modifier E9, which digs openings exactly where they are supposed to be. Implementing this technology was a success in Contiga’s Mandal factory.
Norwegian Contiga, part of Heidelberg Cement, decided to automate their hollow core slab production at their Mandal factory. They wanted to secure orders in the future and gain an edge over their competitors. The factory’s five beds have produced almost 160,000 m2 of slabs annually in recent years. Factory manager Tommy Svensson has been actively involved in the automation process.
“We want to offer high quality products at reasonable prices. The goal of automation was to reduce the amount of heavy manual work in the process and thus save labor costs,” Svensson explains.
The plant has an Elematic’s automatic saw in full operation, and a looper for installing lifting loops in the slabs is being tested. The Modifier E9 operates on four hollow core production lines. It is used for digging openings and recesses and drilling water holes on fresh concrete slabs. It can plot cutting lines, openings and even engrave text onto the slabs.
The Modifier is controlled by the FloorMes system, a part of Elematic Plant Control. The system improves accuracy and reduces the possibility of errors when data is obtained directly from the drawings.
Carefully planning where openings go increase production efficiency
Because Contiga’s hollow core slabs have a lot of openings, the Modifier is undoubtedly useful. Contiga ordered a new Modifier while it was still under development.
“We knew that adopting such a big change would affect the production process and could take time to set up. There were some delays on the way, but we had confidence in Elematic,” Svensson says.
Prior to commissioning, the equipment had to be installed. The Elematic team trained the employees on how to use the new machine. Elematic’s technicians worked to calibrate the machine for a week, but after that, they were ready for production.
According to Svensson, co-operation in adjusting the Modifier for Contiga’s needs was also important. Initially, the design featured unnecessarily large openings, and because the Modifier cleans the bottom of the openings, this slowed the process down.
“The Modifier can clear the opening of debris by about 70%. Most of the time it is enough, as the opening has to be completely clean only in 5-10% of projects, when threaded bars are used instead of corrugated bars.”
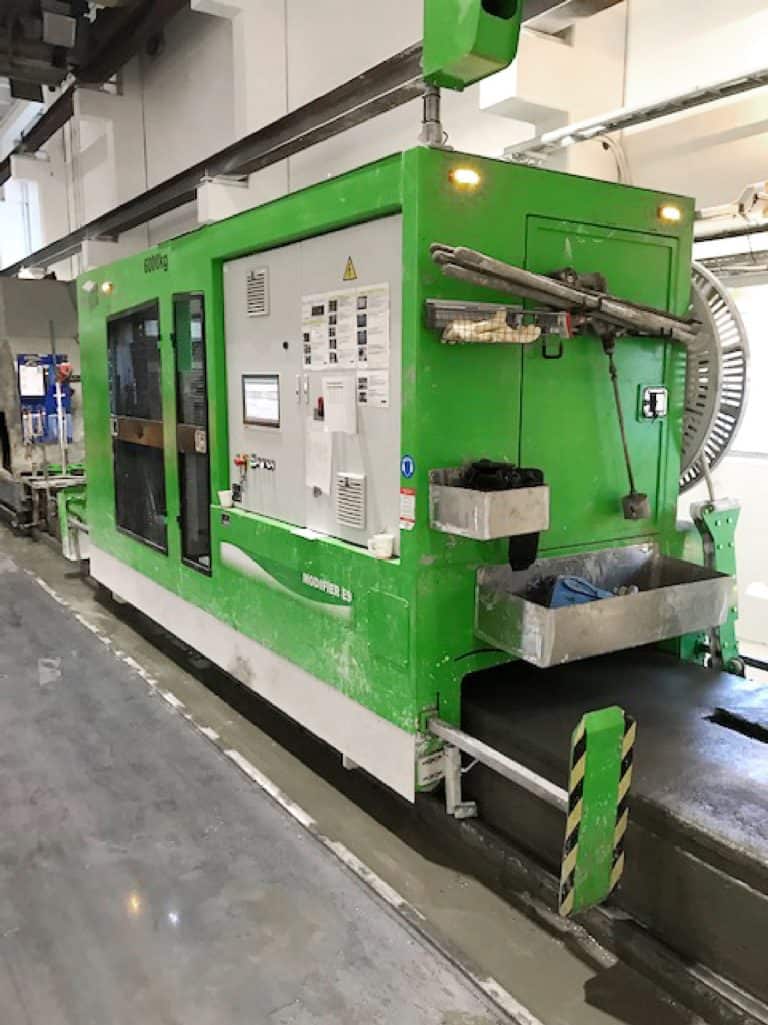
Lighter work and better conditions
The Modifier saves considerable time by eliminating the need for manual marking of cutting lines or for making separate openings for lifting loop installations and through holes. At Contiga, automation using the Modifier E9 not only reduced heavy manual work and labor costs but also eliminated mistakes and improved safety. Some manual work is still needed, to put labels and plastic caps on the slab, for example, but it is physically lighter work.
Svensson already has thoughts on how automation can help save the company even more material. “We are really pleased with the way Elematic helped us move from heavy manual work to using automated machinery. We are currently building a new plant in Bergen and, in addition to the Modifier E9, we have purchased new Extruder E9s there. Then, the Modifier E9 will be able to recycle the excavated concrete directly to the extruder, allowing us to save on material costs.”
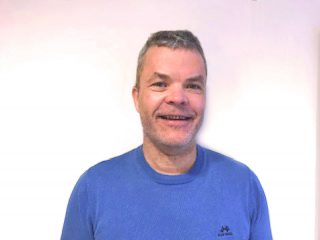
Contiga Mandal’s factory manager Tommy Svensson
Related products
Order our newsletter or contact us!
or