Why sandwich panels?
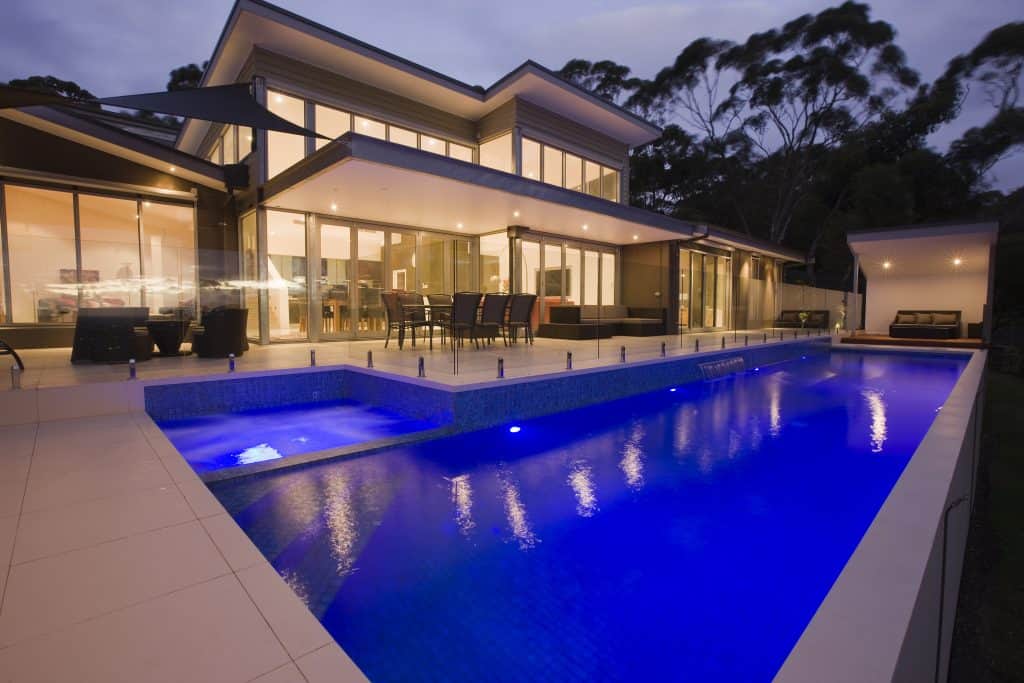
Faced with the prospect of building a house that fronted on to a beautiful piece of bushland above the city of Adelaide in South Australia, I was determined to specify materials that would withstand the conditions. With a typically Mediterranean type climate, the Adelaide Hills area can see heat well into the 40s and strong winds that in winter can reach 100km/hour. I wanted value for money and the best solution for the sloping, and somewhat exposed site.
OK so firstly I need to declare my interest here. I confess that I just may have a natural bias towards precast concrete, because since 2003 I have been the CEO of National Precast Concrete Association Australia.
National Precast is the peak body in Australia representing and promoting precast concrete. After so long, I still love the industry. The individuals are great people. Like me, they are passionate about precast, and together we work vigorously to continue the remarkable growth of precast in Australia and represent its interests.
But because I’ve work for National Precast and have come to love concrete, wasn’t the decider. After all, I was spending my own money here.
After seriously researching almost every other option imaginable for the walls, my decision was clear. Most other construction options didn’t tick all the boxes. What else would deliver resilience to fire, wind and termites, while being energy efficient, but precast sandwich panels? It was an easy decision.
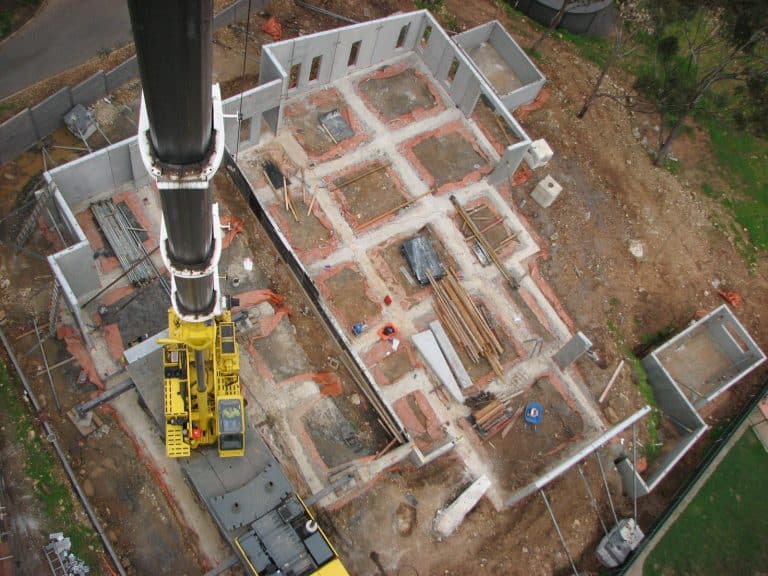
Sandwich panels are an energy-efficient, highly durable and fire resistant solution used largely for exterior walling. Being manufactured off-site and being so thermally efficient, they’ve been used in the UK and Europe for years. My house, however, was to be the first built in South Australia using sandwich panels.
Sandwich panels have three layers: an external non-load bearing concrete layer, a rigid insulation layer and an internal load-bearing concrete layer, which are connected to one another with non-heat-conductive connectors during the casting phase. The panels are used as entire walls, and when erected deliver both the internal and external wall structure.
So how did sandwich panels tick the boxes?
Fire Safety
The house is located in Belair, in the Adelaide Hills, South Australia, which is known for its hot-to-cold climate and danger of bushfires. Because of the location, the house had to be built as fire resistant as possible, but also comfortable to live in. All potential non-combustible options – from double brick, to rendered block and various insulated concrete forms – were thoroughly researched. Precast concrete sandwich panels were the only one that would withstand fire, with my particular walls specified to be fire-rated to four hours.
To further increase the fire resistance, I opted for double glazed and toughened glass windows that have been tested to withstand fire up to 40 kW / m² and a well-insulated and sealed steel roof. In-ground sprinklers and a 95,000 litre rainwater and stormwater tank were also installed to be better prepared in case of fire.
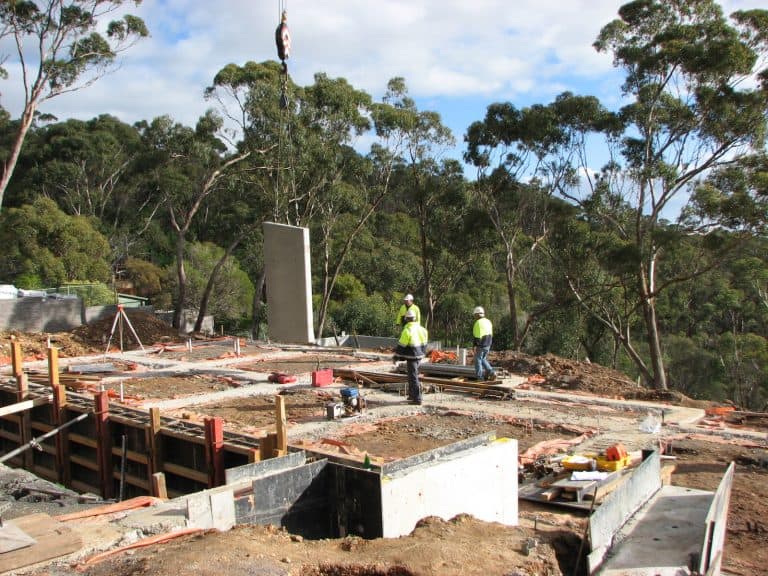
Energy Efficiency
Writer
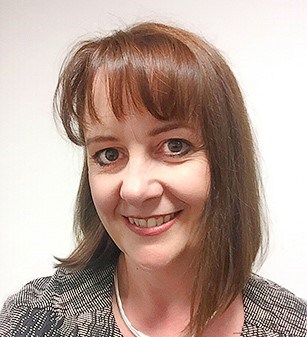
Sarah Bachmann
CEO
National Precast Concrete Association Australia
Sandwich panels take full advantage of the thermal storage properties of concrete to even out temperature extremes inside, when temperatures outside fluctuate from very hot on summer days to cool in the winter nights.
Electricity in South Australia is expensive – probably the most expensive of all Australian States and Territories. So a big objective was to build an energy efficient house, one that would minimize heating and cooling costs. I opted for as many solar passive design elements as possible, to use of the sun’s energy for heating and suitable shading and window orientation. Due to the approximately 100mm thick internal thermal mass of insulated concrete, the sandwich panel walls are efficient in keeping the valuable heat inside the building once they are heated by the winter sun.
Heat is absorbed during the day and then released into the internal living space at night as the outside temperature drops. On the contrary, air-conditioning is needed to a lesser degree during summers, because eaves and other shading block the summer sun from entering windows. The exterior layer absorbs the sun’s heat and the interior layer is protected from the heat by the insulation layer. The interior space therefore remains cool.
In case of longer cold periods, I installed in-floor hydronic heating coils, which further heat the house from the ground up. The solar passive design in combination with the sandwich panels have significantly decreased the cost of heating and cooling.
Cost Efficiency
People have often asked me about the cost of precast in comparison to other more traditional construction materials. Typically, I say that you cannot compare precast with other construction options, unless you accurately factor in all of the associated costs of building with the other options. Costs such as insulation, timber framework, plasterboard, more on-site waste removal and longer construction times must all be factored in. So must the additional heating and cooling costs over the lifetime of the building.
Sandwich panels are manufactured offsite, which means that manufacturing waste is recycled at the factory and installation programmes are quicker. When you live in a house with sandwich panels, you don’t need to run air conditioners and heaters to the same extent. Precast walls are maintenance free, yet they act as permanent barriers to fire, heat, impact and smoke.
Overall, I couldn’t be happier with how the house turned out with sandwich panels. The house design and all its decorative features offer a wonderful living environment and the perfect place to enjoy the wonder of the Australian bush.
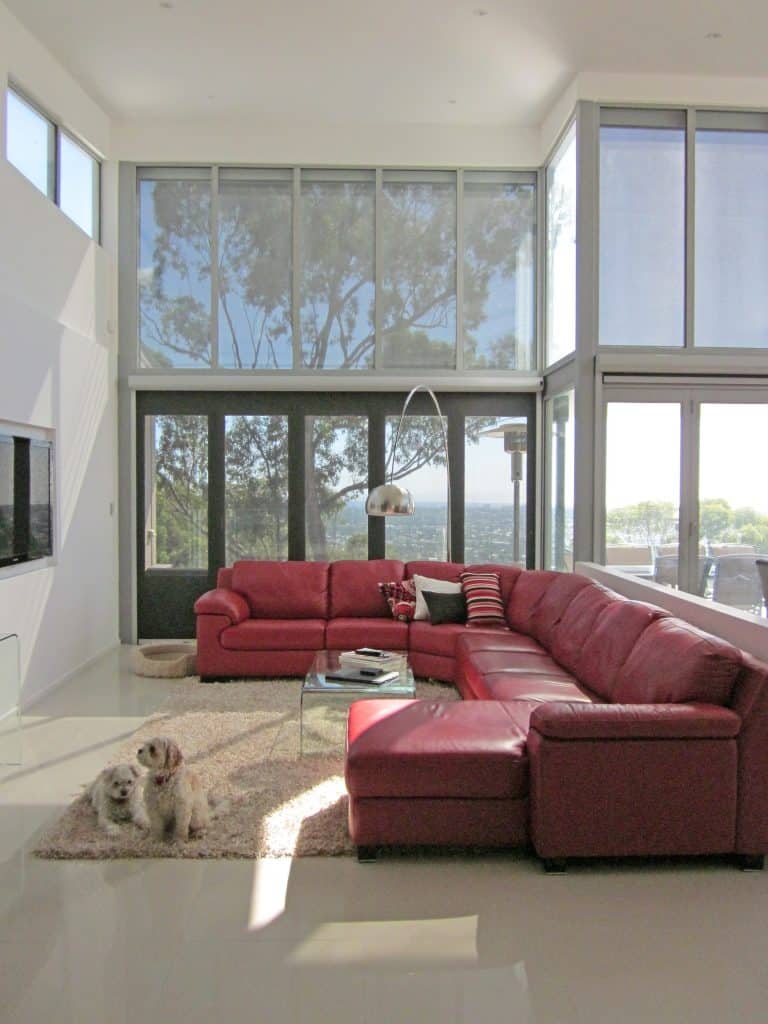
DO YOU HAVE QUESTIONS? CONTACT US!
or