Why millimetres cost in hollow core production
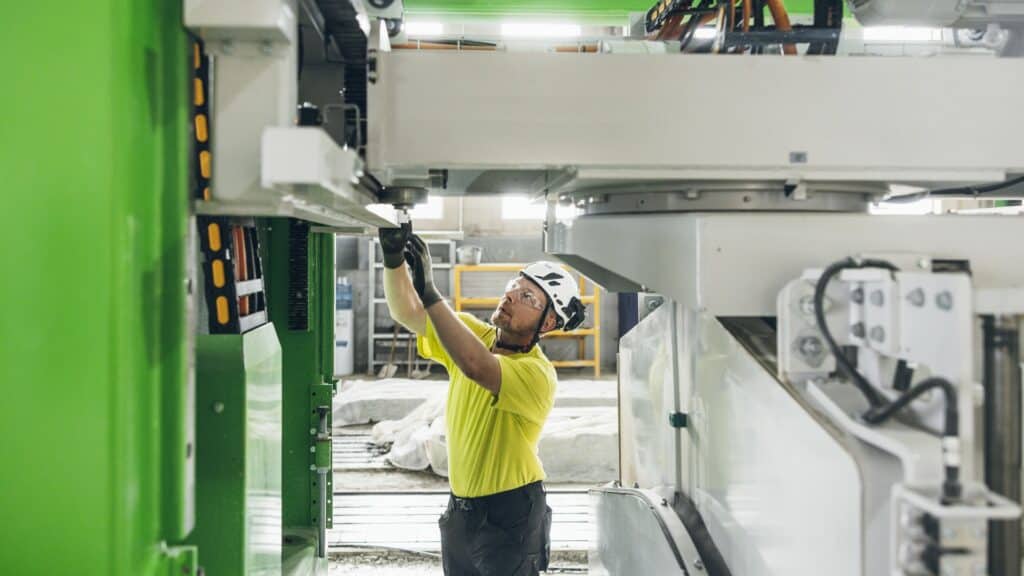
As a precast hollow core manufacturer, you have probably pondered whether to invest in spare and wear parts of original equipment manufacturer or slightly less expensive parts of an external provider. In this blog, I will shed light on the question why it makes sense to keep your millimetres in place in hollow core production – and use those more expensive original parts.
Cross-sections according to the drawings
To start off, when I visit hollow core production lines, I often see slabs, the cross-sections of which do not match the drawings. It is alarming that only a few pay attention to this difference; it is only too easy to turn a blind eye and not see how much concrete will be lost every year. Also, that “wasted” concrete and the amount of money spent on it is difficult to prove, since, unfortunately, people sometimes consider it as a part of the hollow-core slab production process. On the other hand, when ordering spare and wear parts for extruders, it is easy for the purchasing department to put down the numbers and show how some parts are cheaper and big “savings” can be reached when choosing them. But that’s not really the truth.
Save costs by saving concrete
The truth is that you can make the biggest savings in money with savings in concrete as concrete is by far the most expensive part in hollow core slab production. Roughly speaking, concrete / strands account for about 55% of the slab price and wear parts for only 3%. Hence, it is really a no-brainer to see how to make savings if you want to save on production costs.
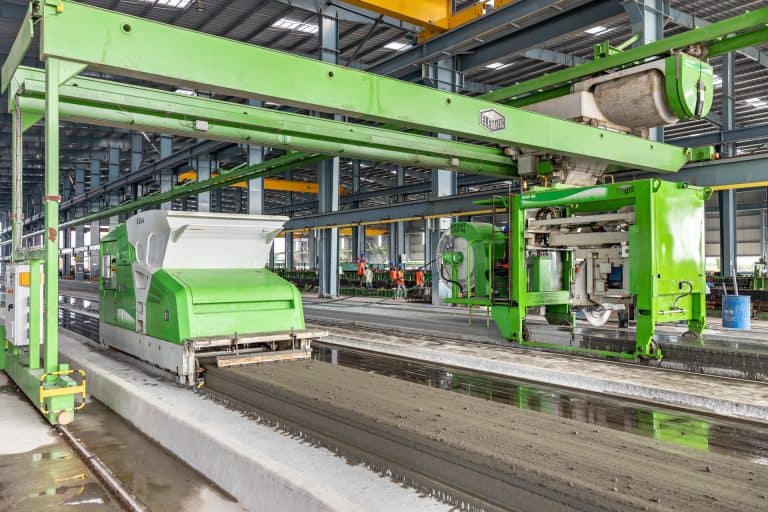
Here are a few examples of what kind of numbers we are talking about:
It hasn’t been long since I visited a factory using copy screws and sleeves. Their six-hole and 200 mm slab cores were 15 mm smaller than the cross section in the drawings. Furthermore, they were happy with the slab. Together, we calculated that they used about 2 cu. m. more concrete on each cast bed compared to a cross section matching with the drawings. This was a shock to them. When casting four beds a day, they wasted 8 cubic meters of concrete – money – every day. This means 48 cubic meters a week, 192 cubic meters a month, and almost 2,500 cubic meters every year. I think this clearly highlights the importance of suitable and properly fitting spares and wears.
Also at the same factory, the extruder settings weren’t the most efficient. Their 200 mm slab height was 206 mm. When we went through this together, we could see that the 6mm oversized slab meant an extra cubic meter pf concrete consumption per bed.
So, the factory used almost 3 cubic meters more concrete per bed than needed. It meant that it was actually expensive to save in spare and wear part purchases.
Conclusion
As said earlier, the savings that come with the right spare parts and proper machine settings. This is hard to realize, though, as these savings do not form a clear sum of money indicated on a particular cost account.
The factory often ends up in the above situation gradually, with no one noticing the slowly rising production costs. The situation is simply accepted, even if the profit drops, and savings are sought from spares and wears. As things get worse, it could be called a negative chain reaction.
So the answer to the initial question – why millimetres are so important in hollow core slab production – is cost savings. Also, when you use original spare parts, it is easy to make the best settings for your extruder.
I will be happy to hear your views and shed more light on the subject. Please contact me!
Writer
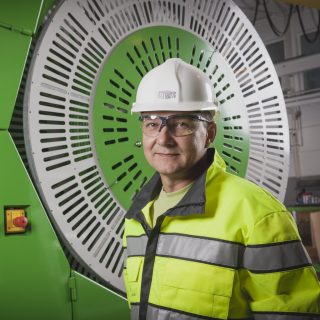
Mikko Hellman
Service Engineer
Customer Service Dubai
Elematic