How to stress efficiently?
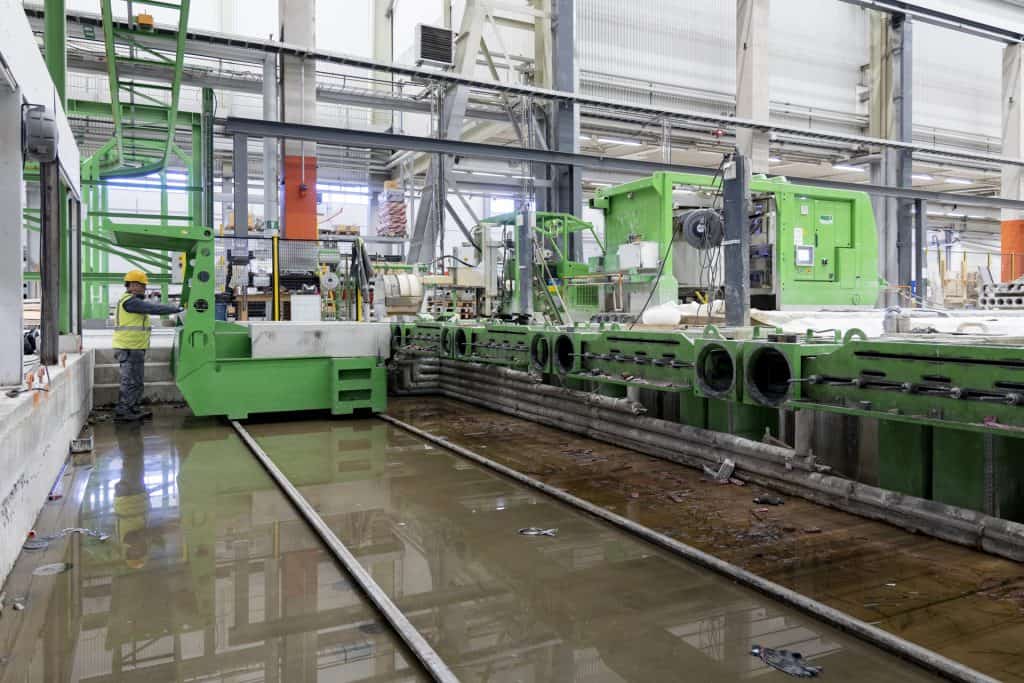
Pre-stressing greatly enhances the structural resilience and load-bearing capacity of precast elements, which is why it is one of the most important steps in hollow-core slab production. Because stressing is such an important and time-consuming step, it is good to know how the process can be made quicker and more efficient. Thus, efficiency is the overruling theme in my blog, where I will approach pre-stressing from three different angles; time savings, strand savings and safety improvements.
Opt for bundle stressing
With the help of Elematic’s Stresser E9, an efficient and safety-improving bundle stressing machine, you can improve pre-stressing safety as well as significantly save both time and strands. How?
Save time
Instead of the single stressing method, you can opt for bundle stressing. Think about it: when using the single stressing method, you spend approximately 2.5 hours for stressing 6 beds, while the same takes only about 30 minutes with a bundle stressing machine. The time difference has clear impacts on the production costs, because when the stressing time decreases, your efficient working time increases. After all, nearly all operations at the plant must be stopped for the time of the stressing process. The savings are reached because the Stresser E9 has been designed for simultaneous pre-stressing of up to 20 strands and 200 tons.
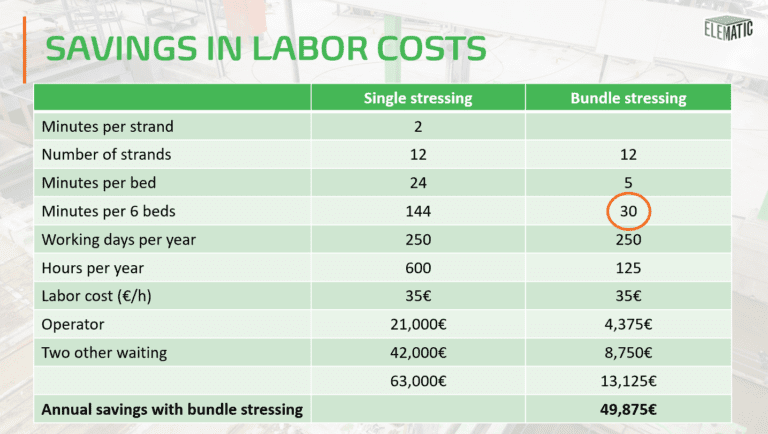
Save strands
While you can save strands by single stressing from the passive end of the bed, the savings aren’t as big as with the bundle stressing method. In both cases, the strand savings come from the fact that the strands are not cut before de-tensioning. Of course, this means that the amount of your strand coils must equal to the amount of the strands that you need to use per slab as well as the beds.
For example, if you save 1.5 meters of strands more per bed by bundle stressing: 1.5 meters x 6 strands x EUR 1 per meter x 6 beds x 250 days = EUR 13,500 per annum. This is the amount of money that would be wasted with the single stressing method.
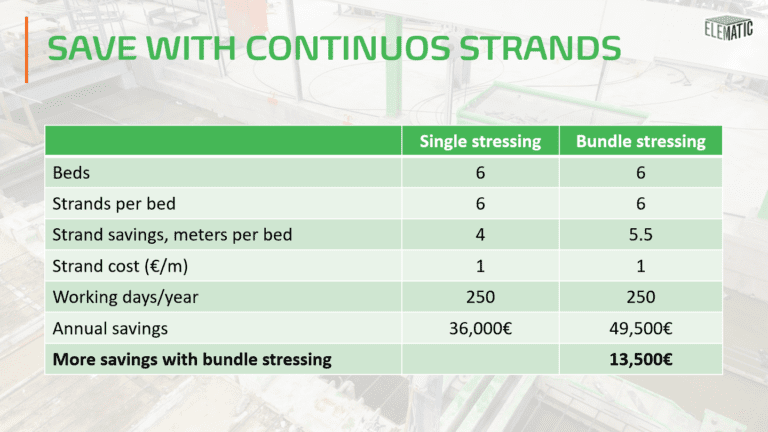
Note: if you aren’t currently using continuous brands for stressing, opting for the bundle stressing method and continuous strands can result in savings of 5 meters per strand. For example, if you save 4 meters of strands with continuous strands: 4 meters x 6 strands x EUR 1 per meter x 6 beds x 250 days = EUR 36,000 per annum.
Improve safety
Safety-wise Stresser E9 is on a new level. The machine features a modern control system with an intuitive user interface that guides the operator through the whole process. This means that by entering the stressing information, the machine calculates the needed distance and moves accordingly. You can also save time by creating a library of predetermined settings for different slab types and strand options, which minimizes the possibility for human errors.
The safety is further increased because the operator needs to sign off the preceding steps from the control panel before moving forward with the process. An example of such can be the attachment of the anchor grips. In addition, the operator constantly has a free view to the danger zone. Thus, they can easily see that the area is clear, and no slippage or other deviation takes place during the pull. Moreover, the system in the Stresser E9 prevents any uneven movement of cylinders and triggers an alarm if the target is not met. However, we still recommend doing quality surveillance with a random sample, the size of which is up to you and the local regulations. The surveillance checks that the stressing target has been achieved with a calibration device. In fact, local construction safety authorities require regular surveillance checks in many countries.
If you are interested in efficient pre-stressing in precast, I will be happy to discuss the topic further. Read more about Stresser E9 here.
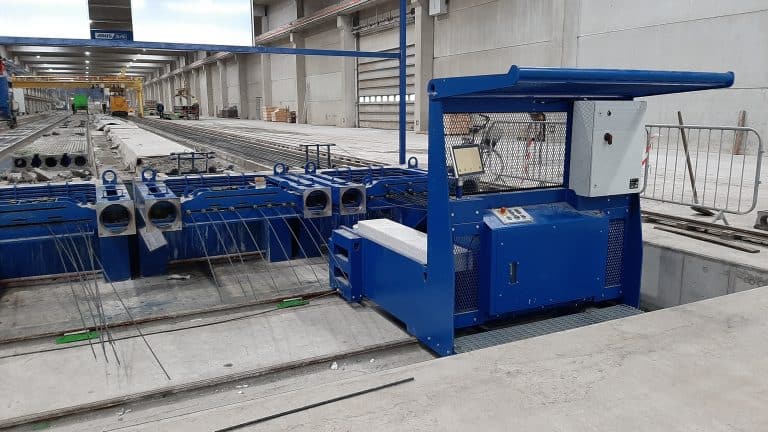
Writer
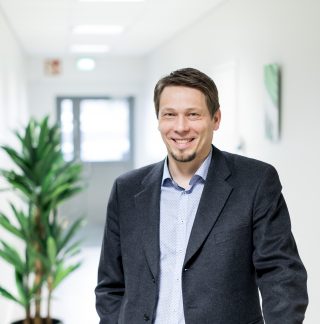
Jani Eilola
Product Director Floor Technologies
Elematic
Let others join this blog too: