How to schedule a precast plant project?
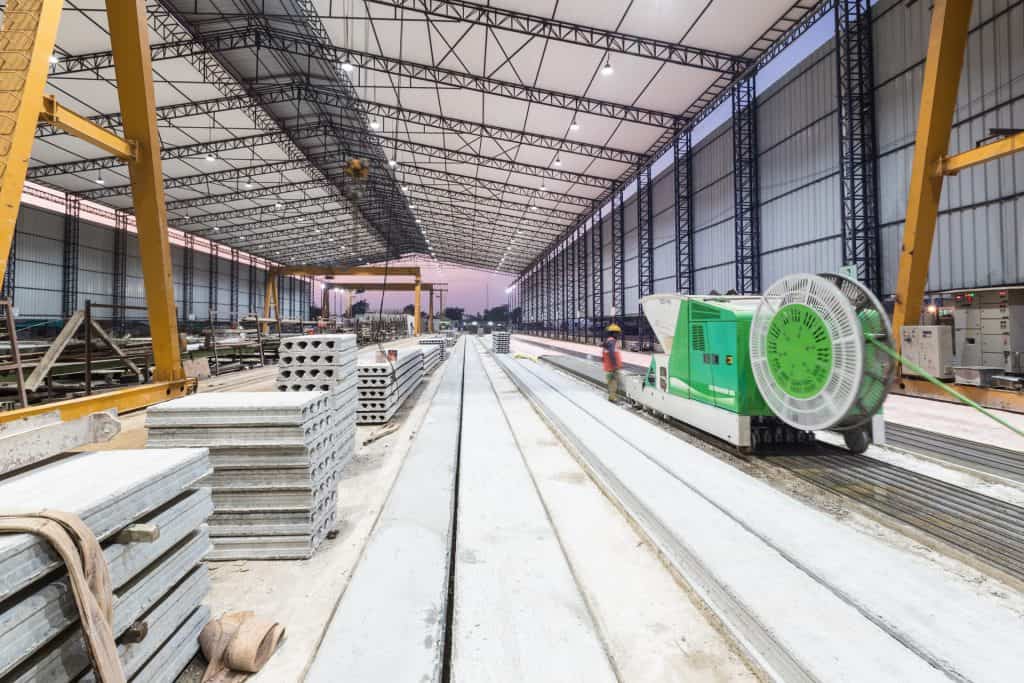
Would you like to set up a precast plant, but aren’t quite sure of the schedule? Are you uncertain of which aspects affect the project and how much time should be reserved for each step? If yes, read about the most important steps while planning and executing a precast factory project.
How the project proceeds
The precast plant project begins with a project launch meeting. Before equipment manufacturing starts, we need to be sure that it suits for the intended use and all technical details are in place; the production capacity, their feedings and even the equipment size. At this point you should provide the actual drawings of the future precast concrete production hall (in dwg., if available). The drawings should include exact technical details of the building, eg. column size, floor levels, hvac points, overhead-crane working areas etc. In other words, detailed info about all the existing structures that are in the new equipment working area.
Based on the drawings, we will create the most suitable layout – or update one from the quotation phase. A carefully designed layout ensures functionality and cost-efficiency of your precast production. We also create equipment drawings to best serve your production needs. This may mean, for example, that the size of a given machine is changed to better fit the preserved location at your factory.
After this, you will receive the initial drawings from us. The drawings include forces to the foundation and columns as well as electrical, water, sewer, compressed air and network feeding points. They allow you to finalize the factory design, i.e. make sure the foundations and all other structures are sturdy enough to handle all the loads.
Even the smallest details matter
In order to create a functional factory, it’s important to have a common understanding of even of the smallest of details. Otherwise there’s a good chance that things go wrong in one way or the other.
To give an example, once we were going through the factory layout with one of our clients. During the meeting we found out that we had planned to put a specific machine to a different hall than where the customer wanted it to go. If we had proceeded with the project without knowing this, the produced machinery could have been unsuitable for the final factory. Sometimes it is also possible that a small change in the layout or in the lifting equipment is the key to further enhance the production flow and thereby add production capacity.
After agreeing on all the details, the equipment design is finalized and the manufacturing can begin. The production schedule is dependable on the size of the factory and the complexity of the equipment, but the average production time for precast plant equipment is 4 months.
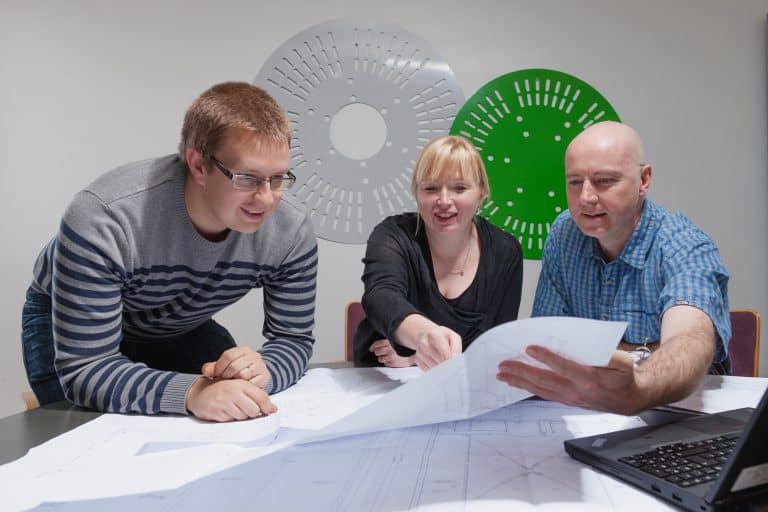
Setting a realistic schedule
Of course, you want to start production as fast as possible, but it’s very important not to set an overly optimistic schedule for all the project steps.
First of all, the production equipment is manufactured based on the overall project schedule. If the installations are delayed for any reason, the equipment must be stored carefully while waiting for the installations to begin. The machinery and all other factory components need to be stored in a clean environment and have a roof over their head. For this you have two options. We can store them at our assembly unit or you can arrange the storing at your end. However, both of these come with extra costs.
Factory installation is precise work
The schedule for the production line installation depends on the schedule of the whole factory, in particular the foundation work. The equipment installation begins after the foundations have been checked for load-bearing capacity by our mechanical supervisor. It’s crucial that the foundations are sturdy and durable enough to bear all the loads from production machinery. It takes a few weeks for the mechanical installations to be completed. After which, your electrical engineers can start their work. Naturally, the time needed for this depends on how many workers you have and how skilled the team – engineers, electricians, mechanics, etc. – is.
Note! The foundations have to be in tolerance. Inaccuracy may prolong the equipment installation work and in the worst case affect the end product negatively!
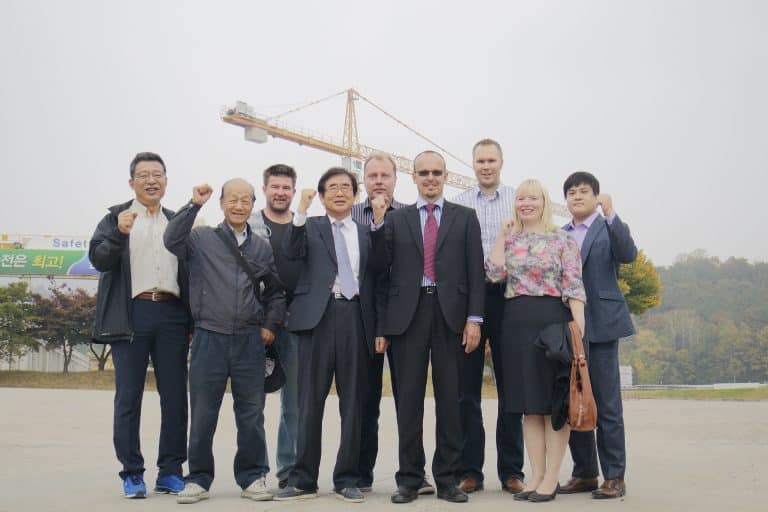
Start-up requires time too
The final step in the precast plant project is taking the machinery into use and testing. This is usually conducted by team of Elematic experts. But that’s not nearly all. Factory operating personnel need to learn how to use the machines. It’s advisable that you name a person responsible for each of the machines. Also, it’s crucial to reserve enough time for training. Your machines will stay in a better condition, when people know how they are used and what kind of maintenance is required. Hence, we recommend coming up with a maintenance program and a dedicated maintenance team. We can help you too with a preventive maintenance program.
In addition, finding the ideal and most cost-efficient concrete mix that works with the equipment always requires local testing. This phase can be very fast if the concrete mix has been well-thought-through in advance. But it may also be a time-consuming process. Thus, we recommend not taking on too many projects for the time of the factory start-up. This way you won’t make any of your future customers angry before the first delivery.
Efficient cooperation is the key
Cooperation and efficient communication is a crucial part of any project, especially when parties locate in different countries, on different continents. The complete precast plant is planned and the machinery is manufactured based on your exact factory measurements. These include; height, length, width and places for columns, to mention a few. Hence, let us know of even the smallest changes. We are here to help you! With thorough planning, a precast plant can be set-up in a quick time frame.
We offer lifetime commitment. Therefore, the project manager is responsible for your factory until the end of the warranty period. After that, our customer service will start taking care of you, and they will be your first point of contact. They will help you to solve all production related problems and give advice on how to further enhance the processes. Once again, cooperation is the key – let’s rock the precast world together!
Writer
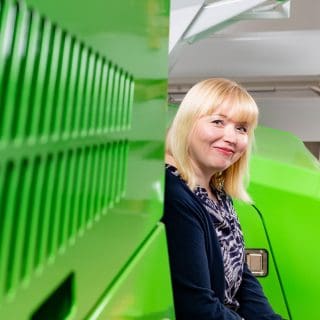
Maija Toivonen
Project Manager
Elematic