5 steps we take to make sure your factory performs as it should
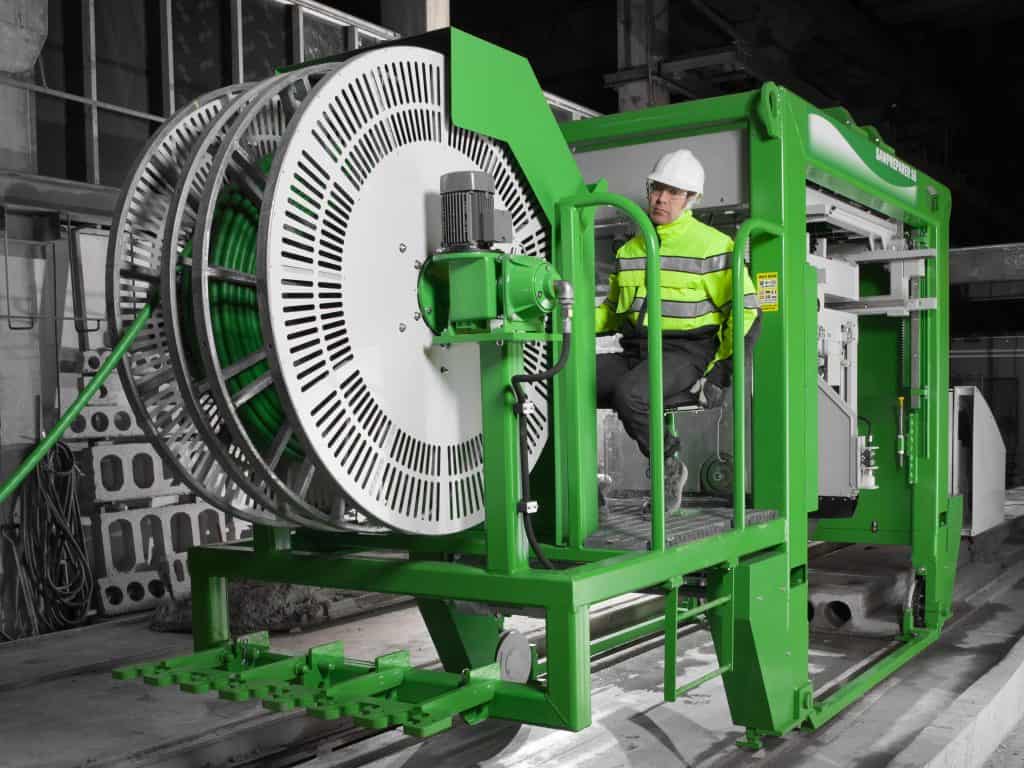
Have you ever pondered how high quality of machines can be ensured at the factory? Where do the risks lie and what measures are taken to avoid those? How do quality inspections, at our end, affect your production? Everyone wants the production to be as cost-efficient as possible without compromising the quality. We at Elematic pay close attention to the manufacturing process as we want everything to run as smoothly as possible once the machine arrives at your site. This is what we do:
1. Organizing guidelines & training for the network of subcontractors and auditing
It’s essential that the production capability (e.g. skills of the personnel, production facilities, machines and quality processes) of our subcontractors meets the set quality requirements. Therefore, our long-term subcontracting partners are audited regularly. In the case of a new subcontractor, auditing and training is organized before the manufacturing can begin. We go through the process and the expectations together to ensure that everybody shares the same view and knows what the target is.
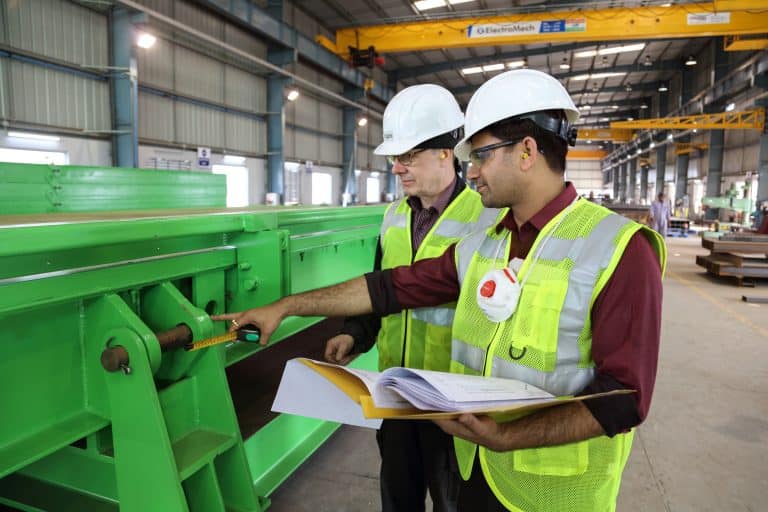
To give an example, when a new subcontractor is chosen to deliver a part for a machine, making the order and sending the needed technical documentation aren’t nearly the only steps taken. The best possible manufacturing, surface finishing, inspection and packing methods are also defined and agreed on together with the subcontractor. Because of this approach, we can be sure that the manufacturer understand the requirements and does everything they can to avoid manufacturing errors.
2. Systematically inspecting the goods
Ready and semi-finished products, such as cast iron pieces, are inspected when delivered to our warehouse. The risk of a quality error occurring during the manufacturing process rises when the subcontractor is new or an existing partner starts to manufacture new products.
In those cases, systematical checking is conducted to catch all faulty parts before the products are sent further to our customers or used for device assembly.
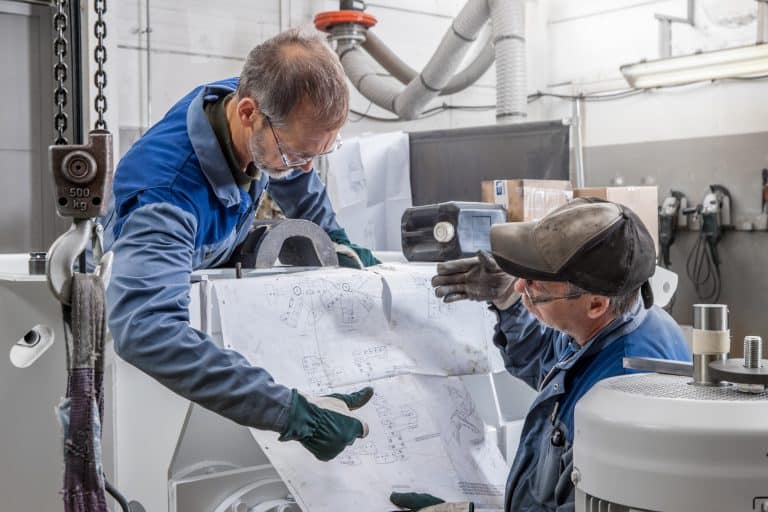
3. Methodically handling errors
Immediately after spotting an error, we resolve the reasons behind it and take the corrective actions required. We make sure that the damage is minimized by checking that such parts aren’t stored in our warehouse or at the subcontractor’s and that faulty parts haven’t been sent to customers. These measures are taken to prevent similar mistakes from occurring again.
For instance, once an inspector spotted that Extruder’s hollow-core sleeve was too wide when it arrived to the warehouse. It would have resulted in the holes of hollow-core slabs being also too wide. Further, it would have massively decreased the slabs loading capacity.
We sent the faulty part to the supplier to be fixed. The reason for the error was tracked based on which we changes the processes and clarified the work instructions.
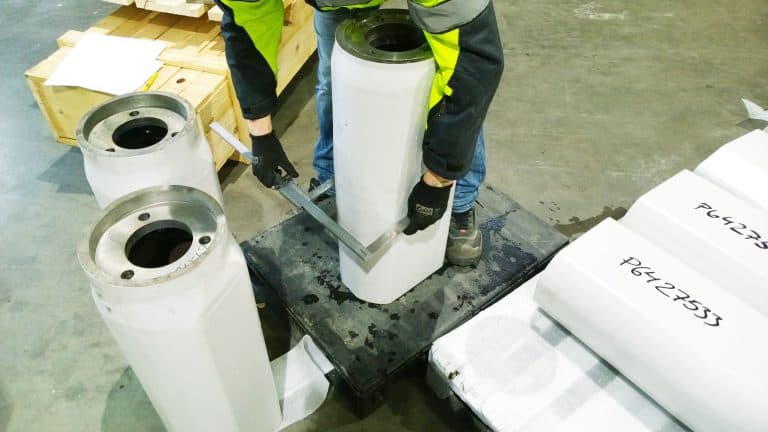
4. Standardized feedback handling
We collect feedback from our employees, customers and other stakeholders. The feedback is handled systematically to reach better outcomes in the future.
When a technical feedback is received, we investigate whether the problem is connected to the design or the manufacturing. Then an expert finds out how the root cause needs to be corrected in the field. The implementation schedule is decided based on the urgency of the error. They also monitor that the corrective actions are implemented accordingly. Further faulty parts are also removed from the warehouse.
5. Constantly developing the processes
We constantly develop our processes based on the received feedback and systematic observation. When a bottle neck is spotted, we will remove it.
Quality matters, hence the processes to ensure high quality must be constantly developed. We, together with our professional partners and subcontractors, aim at delivering flawless, high-quality machines that will last for years to come.
Writer
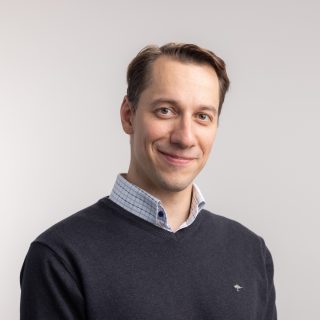
Toni Koitmaa
Quality Manager
Elematic